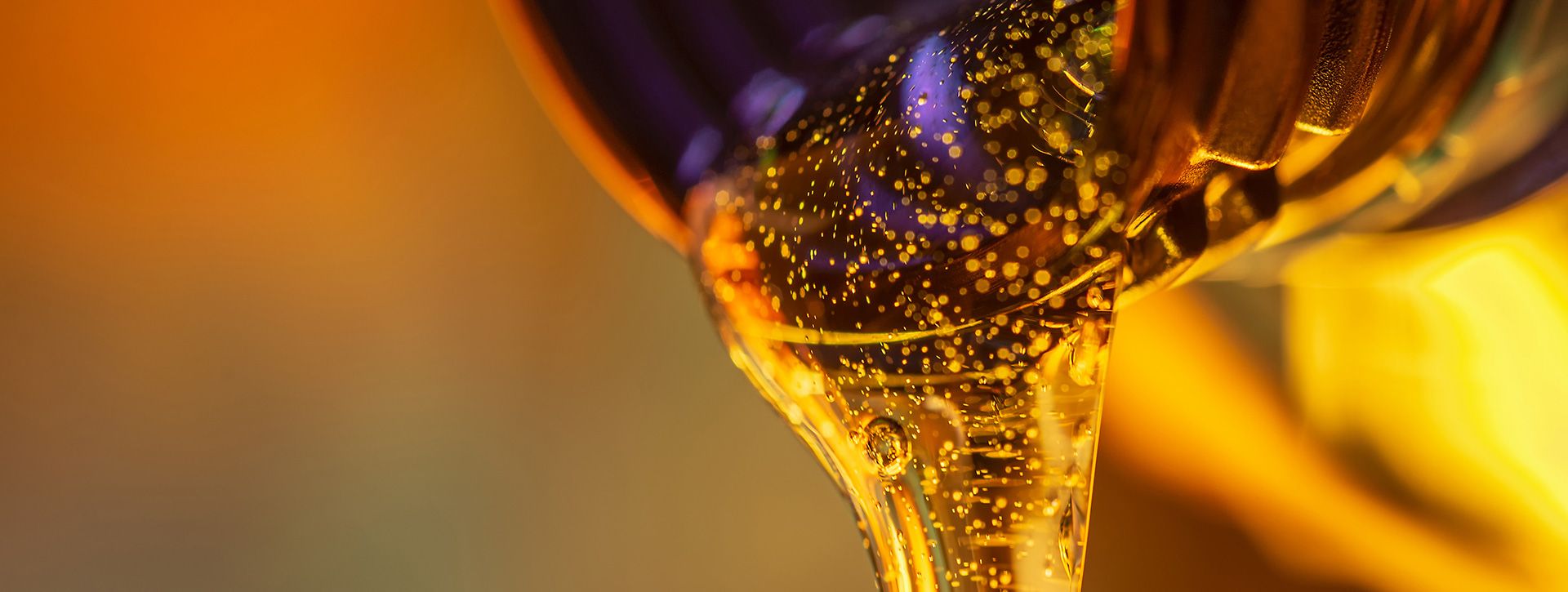
Failure Analysis of Anti-wear Hydraulic Oil Additive Package
The anti-wear hydraulic oil additive package plays a crucial and vital role in industrial hydraulic systems. It can effectively reduce the wear of hydraulic components and ensure the stable operation of the hydraulic system. However, in practical use, the anti-wear hydraulic oil additive package may fail due to various reasons, resulting in a decline in the performance of the hydraulic system and even causing equipment failures. Therefore, conducting a failure analysis of the anti-wear hydraulic oil additive package, accurately identifying the causes of failure, and taking corresponding preventive measures are of great significance for extending the service life of the anti-wear hydraulic oil additive package and ensuring the reliable operation of the hydraulic system.
I. Common Failure Causes
(1) Oxidation Failure
The base oil and additives in the anti-wear hydraulic oil additive package will undergo an oxidation reaction with the oxygen in the air during long-term use. The oxidation reaction will produce harmful substances such as acidic substances, gums, and asphaltenes. These substances will reduce the lubricating performance of the anti-wear hydraulic oil additive package, increase the viscosity of the oil, block the filters and oil passages, and thus lead to the failure of the anti-wear hydraulic oil additive package.
The factors affecting the oxidation reaction mainly include temperature, oxygen concentration, metal catalysis, and time. The higher the temperature, the faster the oxidation reaction rate; the higher the oxygen concentration, the more severe the oxidation reaction; the metal surface, such as the metal components in the hydraulic system, will catalyze the oxidation reaction and accelerate the oxidation process; the longer the service time, the more opportunities the anti-wear hydraulic oil additive package has to contact with oxygen, and the more severe the oxidation reaction will be.
(2) Contamination Failure
Solid Particle Contamination
Solid particles are one of the most common contaminants in the anti-wear hydraulic oil additive package, mainly including metal wear debris, dust, sand grains, and seal material fragments. These solid particles will enter various components of the hydraulic system, such as pumps, valves, and hydraulic cylinders, along with the flow of the hydraulic oil, causing wear, scratching, and blockage of the components. When the size of the solid particles is larger than the fit clearance of the hydraulic components, it will lead to increased friction between the components and accelerated wear, thus reducing the service life of the hydraulic components; when the solid particles block the filter, it will cause an increase in the pressure drop of the filter and a decrease in the oil flow rate, affecting the normal operation of the hydraulic system.
The sources of solid particle contamination mainly include impurities remaining during the manufacturing and installation of the hydraulic system, wear debris generated by the wear of hydraulic components, and dust and sand grains in the external environment entering the oil through the tank breather hole or poor seals.
Moisture Contamination
The entry of moisture into the anti-wear hydraulic oil additive package will have a serious impact on its performance. Water will react with the additives in the anti-wear hydraulic oil additive package, damaging the structure of the additives and reducing their performance; water will also cause the corrosion of hydraulic components. Especially in a humid environment, the contact between moisture and the metal surface will form electrochemical corrosion, accelerating the corrosion and damage of metal components; in addition, moisture will emulsify the anti-wear hydraulic oil additive package, forming an emulsion, reducing the lubricating and cooling performance of the oil.
The sources of moisture contamination mainly include poor sealing of the hydraulic system, allowing external moisture to enter the oil; the tank breather hole not being equipped with an effective moisture-proof device, allowing moisture in the air to enter the tank; and during the shutdown process of the hydraulic system, due to the decrease in temperature, condensed water is formed inside the tank.
Contamination by Other Oils
During the maintenance and servicing of the hydraulic system, if other oils that are incompatible with the anti-wear hydraulic oil additive package are mistakenly added, such as hydraulic oils of different brands and models, or lubricating oils and gear oils, etc., it will lead to a decline in the performance of the anti-wear hydraulic oil additive package and even failure. The chemical components of different oils may react with each other, generating precipitates and gums, blocking the filters and oil passages; at the same time, the viscosity, flash point, oxidation resistance, and other indicators of different oils may be different and cannot meet the working requirements of the hydraulic system, thus affecting the normal operation of the hydraulic system.
(3) Additive Failure
The anti-wear hydraulic oil additive package contains various additives, such as anti-wear agents, antioxidants, preservatives, and antifoaming agents. These additives play their respective roles in the oil and jointly ensure the performance of the anti-wear hydraulic oil additive package. However, the additives will gradually be consumed during use. When the content of the additives decreases to a certain extent, the performance of the anti-wear hydraulic oil additive package will decline, and failure will occur.
The reasons for additive failure mainly include the volatilization, decomposition, and adsorption of additives. In a high-temperature environment, additives are likely to volatilize, resulting in a decrease in their content; during long-term use, additives will undergo chemical reactions with other components in the oil and decompose and fail; in addition, additives will also be adsorbed by the filters, seal materials, etc. in the hydraulic system, resulting in a decrease in their effective content.
(4) Hydrolysis Failure
Some additives in the anti-wear hydraulic oil additive package, such as ester-based anti-wear agents and rust inhibitors, are prone to undergo a hydrolysis reaction in the presence of water. The hydrolysis reaction will produce acidic substances and alcohols, which will corrode the hydraulic components and reduce the performance of the anti-wear hydraulic oil additive package. The rate of the hydrolysis reaction is related to factors such as temperature, moisture content, and the type of additive. The higher the temperature and the higher the moisture content, the faster the hydrolysis reaction rate.
(5) High-temperature Failure
During the operation of the hydraulic system, due to the friction of hydraulic components, pressure loss, and other reasons, a large amount of heat will be generated, causing the temperature of the anti-wear hydraulic oil additive package to rise. When the temperature exceeds the applicable temperature range of the anti-wear hydraulic oil additive package, the oil will undergo oxidation, decomposition, volatilization, and other phenomena, resulting in a decrease in the viscosity of the oil, a decrease in the flash point, and an increase in the acid value, thus causing the anti-wear hydraulic oil additive package to fail. High temperature will also accelerate the failure of additives and reduce their performance.
(6) Mechanical Factor Failure
Mechanical components in the hydraulic system, such as pumps, valves, and hydraulic cylinders, will generate vibrations and impacts during operation. These mechanical factors will cause the bubbles in the anti-wear hydraulic oil additive package to burst, resulting in cavitation phenomena, thus forming local high temperatures and high pressures, causing the oil to oxidize and decompose and generating harmful substances. In addition, the wear and looseness of mechanical components will also lead to the contamination and leakage of the anti-wear hydraulic oil additive package, affecting its performance and service life.
II. Detection Methods for Failure Analysis
(1) Spectral Analysis
Spectral analysis is a commonly used detection method for failure analysis, mainly used to detect the content and types of metal elements in the anti-wear hydraulic oil additive package. Through spectral analysis, it is possible to determine which components in the hydraulic system have undergone wear, as well as the degree and type of wear. For example, when the content of iron elements increases, it may indicate that components such as the hydraulic pump or hydraulic cylinder have undergone wear; when the content of copper elements increases, it may indicate that valve components have undergone wear.
The principle of spectral analysis is to utilize the absorption and emission characteristics of substances to light of different wavelengths. By introducing a sample of the anti-wear hydraulic oil additive package into a spectrometer, the atoms or molecules in the sample are excited to emit light of specific wavelengths. Then, by detecting the intensity and wavelength of this light, the content and types of metal elements in the sample can be determined.
(2) Viscosity Detection
Viscosity is one of the important performance indicators of the anti-wear hydraulic oil additive package, which directly affects the lubricating and flowing performance of the oil. Through viscosity detection, it is possible to determine whether the viscosity of the anti-wear hydraulic oil additive package meets the usage requirements and whether failure phenomena such as oxidation and contamination have occurred. When the anti-wear hydraulic oil additive package undergoes oxidation, large-molecule gums and asphaltenes will be generated, resulting in an increase in the viscosity of the oil; when the oil is contaminated, such as containing solid particles or moisture, it will cause the viscosity of the oil to change.
The main methods for viscosity detection include the capillary viscometer method and the rotational viscometer method. The capillary viscometer method calculates the viscosity by using the flow time of the liquid in the capillary, which has the advantages of simple operation and high precision; the rotational viscometer method measures the viscosity by using the resistance of the rotating body in the liquid and is suitable for measuring the viscosity of high-viscosity liquids.
(3) Acid Value Detection
The acid value is an indicator for measuring the content of acidic substances in the anti-wear hydraulic oil additive package, which reflects the degree of oxidation and contamination of the oil. When the anti-wear hydraulic oil additive package undergoes oxidation, acidic substances will be generated, resulting in an increase in the acid value; when the oil is contaminated by moisture, the moisture will react with the additives to generate acidic substances, which will also cause the acid value to increase. Through acid value detection, it is possible to determine the degree of oxidation and contamination of the anti-wear hydraulic oil additive package and take corresponding measures in a timely manner.
The main methods for acid value detection include the potentiometric titration method and the indicator titration method. The potentiometric titration method determines the titration end point by using the response of the electrode to the hydrogen ion concentration in the solution, which has the advantages of high precision and high automation; the indicator titration method determines the titration end point by using the color change of the indicator at different pH values, which is simple to operate but has relatively low precision.
(4) Moisture Detection
Moisture detection is an important method for determining whether the anti-wear hydraulic oil additive package is contaminated by moisture. Commonly used moisture detection methods include the Karl Fischer method, the distillation method, and the infrared spectroscopy method. The Karl Fischer method is a classic moisture detection method, which has the advantages of high precision and a wide application range and can detect trace amounts of moisture; the distillation method heats and distills the sample of the anti-wear hydraulic oil additive package, evaporates the moisture, and then collects the moisture through condensation to measure the moisture content, which is suitable for detecting samples with a relatively high moisture content; the infrared spectroscopy method detects the moisture content by using the absorption characteristics of moisture to infrared light, which has the advantages of being fast and non-destructive.
(5) Particle Counting
Particle counting is an important method for detecting the degree of solid particle contamination in the anti-wear hydraulic oil additive package. Through particle counting, it is possible to determine the number, size, and distribution of solid particles in the oil and judge the severity of the contamination. Commonly used particle counting methods include the light obscuration method and the resistive method. The light obscuration method detects the number and size of particles by using the blocking effect of particles on light, which has the advantages of fast detection speed and high precision; the resistive method detects the number and size of particles by using the resistance change caused when particles pass through a small hole and is suitable for detecting conductive particles.
(6) Infrared Spectroscopy Analysis
Infrared spectroscopy analysis can be used to detect the changes in the chemical composition of the anti-wear hydraulic oil additive package and determine whether failure phenomena such as oxidation and hydrolysis have occurred in the oil. By measuring the infrared spectrum of the anti-wear hydraulic oil additive package sample and comparing it with the infrared spectrum of the fresh oil, it is possible to analyze whether new functional groups, such as carbonyl groups and hydroxyl groups, have been generated in the oil, thereby determining the type and degree of failure of the oil.
(7) Thermogravimetric Analysis
Thermogravimetric analysis is a method for studying the mass change of the anti-wear hydraulic oil additive package during the heating process, mainly used to detect the thermal stability and oxidation resistance of the oil. Through thermogravimetric analysis, parameters such as the decomposition temperature, weight loss rate, and residue amount of the oil at different temperatures can be determined, and the high-temperature resistance and service life of the oil can be evaluated.
(8) Elemental Analysis
Elemental analysis can detect the content of various elements in the anti-wear hydraulic oil additive package. In addition to metal elements, it also includes non-metal elements such as sulfur, phosphorus, and nitrogen. Through elemental analysis, it is possible to understand the content and distribution of additives and determine whether the additives have failed or been completely consumed.
(9) Simulation Test
The simulation test is to simulate the working environment and operating conditions of the hydraulic system under laboratory conditions and conduct performance tests and failure analysis on the anti-wear hydraulic oil additive package. For example, working conditions such as high temperature, high pressure, and high speed can be simulated, and the performance changes and failure phenomena of the anti-wear hydraulic oil additive package can be observed, and the causes of failure can be analyzed to provide a reference for practical applications.
III. Preventive Measures and Improvement Suggestions for Failure
(1) Reasonable Selection of Anti-wear Hydraulic Oil Additive Package
When selecting an anti-wear hydraulic oil additive package, it is necessary to choose the appropriate model and specification according to the working conditions of the hydraulic system, such as working pressure, temperature, rotational speed, and environment. It is necessary to select a brand with reliable quality and good reputation to ensure that the performance of the anti-wear hydraulic oil additive package meets the usage requirements. At the same time, it is necessary to pay attention to the compatibility of the anti-wear hydraulic oil additive package and avoid mixing it with other oils.
(2) Strengthen the Cleaning and Maintenance of the Hydraulic System
During the installation and commissioning of the hydraulic system, it is necessary to ensure the cleanliness inside the system and remove the remaining impurities and contaminants. Clean and inspect the hydraulic components to ensure that there is no oil stain, dust, or metal debris on the surface of the components.
Replace the hydraulic oil filter regularly to promptly remove the solid particles and contaminants in the oil. Reasonably determine the replacement cycle of the filter according to the working environment of the hydraulic system and the degree of oil contamination.
Clean the hydraulic system regularly to remove the gums, asphaltenes, and precipitates inside the system. Use special cleaning agents during cleaning to avoid damaging the hydraulic components.
(3) Control the Working Temperature of the Hydraulic System
Reasonably design the heat dissipation devices of the hydraulic system, such as radiators and coolers, to ensure that the hydraulic system operates within the normal working temperature range. Select appropriate heat dissipation devices according to the power of the hydraulic system and the working environment to ensure the heat dissipation effect.
Regularly check the working status of the heat dissipation devices and promptly clean the dust and debris on the surface of the radiators to ensure the heat dissipation efficiency.
Avoid the long-term operation of the hydraulic system in a high-temperature environment. For example, in the hot summer season, effective cooling measures should be taken, such as increasing the rotational speed of the cooling fan and reducing the load of the hydraulic system.
(4) Prevent Moisture and Other Contaminants from Entering the Hydraulic System
Strengthen the sealing performance of the hydraulic system, regularly check the wear and aging of the seals, and promptly replace the damaged seals. In particular, for the sealing of the tank, it is necessary to ensure that the tank breather hole is equipped with an effective moisture-proof device to prevent external moisture and dust from entering the tank.
During the maintenance and servicing of the hydraulic system, pay attention to the operation specifications to avoid the entry of moisture and other contaminants into the oil. For example, when adding the anti-wear hydraulic oil additive package, use clean tools and containers to prevent impurities from being introduced into the oil; when overhauling the hydraulic components, keep the working environment clean to avoid the entry of dust and sand grains into the system.
Regularly conduct moisture detection on the anti-wear hydraulic oil additive package. When moisture is found in the oil, promptly take dehydration measures, such as using a vacuum oil filter and other equipment to dehydrate the oil.
(5) Regularly Detect and Replace the Anti-wear Hydraulic Oil Additive Package
Formulate a reasonable detection cycle and regularly detect the performance indicators of the anti-wear hydraulic oil additive package, such as viscosity, acid value, moisture, and particle count. Through the detection results, promptly understand the performance changes and failure situations of the oil to provide a basis for the replacement of the oil.
Reasonably determine the replacement cycle according to the usage situation and detection results of the anti-wear hydraulic oil additive package. Do not wait until the oil completely fails before replacing it to avoid causing failures and damage to the hydraulic system.
(6) Optimize the Formula and Production Process of the Anti-wear Hydraulic Oil Additive Package
For the manufacturers of the anti-wear hydraulic oil additive package, it is necessary to continuously optimize the product formula to improve the oxidation resistance, contamination resistance, and high-temperature resistance of the anti-wear hydraulic oil additive package. At the same time, it is necessary to improve the production process to ensure the stable and reliable quality of the product. For example, add high-efficiency antioxidants and anti-wear agents to the formula to improve the service life of the oil; adopt advanced production equipment and purification processes to reduce the pollution during the production process.
(7) Strengthen the Training and Management of Operators
The operation level and maintenance awareness of operators have an important impact on the service life of the anti-wear hydraulic oil additive package and the reliable operation of the hydraulic system. Therefore, it is necessary to strengthen the training of operators to make them familiar with the working principle of the hydraulic system, the performance characteristics and maintenance requirements of the anti-wear hydraulic oil additive package, and master the correct operation methods and maintenance skills. At the same time, it is necessary to establish a sound management system, clarify the responsibilities and authorities of operators, and ensure the effective implementation of various maintenance measures.
Conclusion
The failure analysis of the anti-wear hydraulic oil additive package is a complex and important task. Through the analysis of common failure causes and the application of failure analysis detection methods, the causes of failure of the anti-wear hydraulic oil additive package can be accurately identified, and corresponding preventive measures and improvement suggestions can be taken. Measures such as the reasonable selection of the anti-wear hydraulic oil additive package, strengthening the cleaning and maintenance of the hydraulic system, controlling the working temperature, preventing the entry of contaminants, regularly detecting and replacing the oil, optimizing the formula and production process, and strengthening the training of operators can effectively extend the service life of the anti-wear hydraulic oil additive.
The Price of Hydraulic Oil Additives Package
The price of Hydraulic Oil Additives Package varies depending on factors such as brand, specification, composition, and sales channels. If you are interested in Hydraulic Oil Additives Package, please feel free to contact us.
Supplier of Hydraulic Oil Additives Package
UNPChemicals is a professional supplier of high-quality and effective Hydraulic Oil Additives Package. We offer several remarkable products, namely High zinc hydraulic oil additives UNP AH502A,Low Zinc Hydraulic Oil Additives UNP AH502B,Zinc-free Hydraulic Oil Additives UNP AH502C,etc.
High zinc hydraulic oil additives UNP AH502A are a type of chemical additive used in hydraulic oils that contain high levels of zinc dialkyldithiophosphate (ZDDP). ZDDP is a well-known anti-wear agent that also provides antioxidant, anti-corrosion, and anti-foam properties. The zinc in these additives plays a crucial role in forming a protective film on metal surfaces within the hydraulic system, thereby reducing wear and extending the life of the system components.
Low Zinc Hydraulic Oil Additives UNP AH502B are a class of advanced lubricant additives designed to enhance the performance of hydraulic oils with reduced zinc content.These additives are formulated to provide a balance of anti-wear,extreme pressure,and antioxidant properties,making them suitable for modern hydraulic systems that demand high performance with lower environmental impact.
Zinc-free Hydraulic Oil Additives UNP AH502C are a new class of environmentally friendly lubricant additives designed for hydraulic systems.These additives are formulated to provide the same level of performance as traditional zinc-containing additives but without the heavy metal content,reducing the environmental impact of hydraulic fluids.
Professional Lubricant Additive Manufacturer
UNPChemicals,aka Luoyang Pacific United Petrochemical Co., Ltd., focuses on the application and development of special lubricating grease additives such as MODTC, MODTP, molybdenum amide, thiadiazole metal deactivators, and phosphate esters. With nearly 30 products in seven series, including extreme pressure anti-wear additives and special grease additives, it is a global manufacturer of special lubricating grease additives and a national high-tech enterprise with great influence and leading role in the industry. If you are looking for Lubricant Additive or technical information, feel free to contact UNPChemicals.