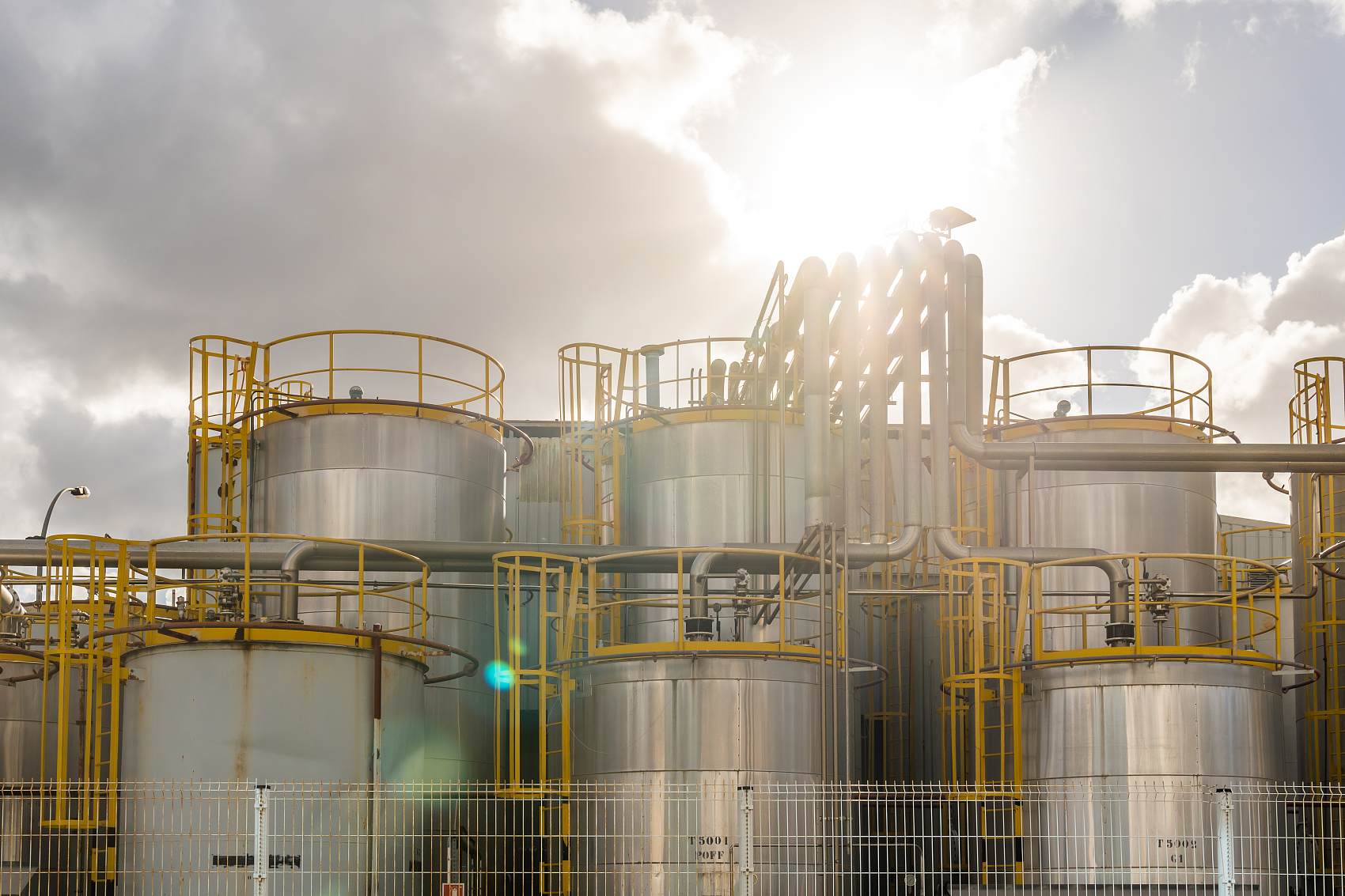
Optimization and Application Expansion of Hydraulic Oil Composite Additives
In the modern industrial system, hydraulic systems, as core components for transmitting power and controlling actions, are widely used in various fields such as engineering machinery, aerospace, and intelligent manufacturing. Hydraulic oil, as the "blood" of hydraulic systems, its performance directly affects the operating efficiency, stability, and service life of the system. Hydraulic oil composite additives, as a key component to improve the performance of hydraulic oil, can significantly enhance core indicators such as wear resistance, oxidation resistance, and anti-emulsification properties of hydraulic oil through scientific compounding of various functional additives, thereby ensuring the reliable operation of hydraulic systems under complex working conditions. With the continuous upgrading of industrial technology, the performance requirements for hydraulic systems are increasingly high, which also promotes hydraulic oil composite additives to develop towards better performance and wider application range. Therefore, in-depth research on the performance optimization methods of hydraulic oil composite additives and active expansion of their application fields are of great significance for promoting the high-quality development of modern industry.
The basic properties of hydraulic oil composite additives are the foundation for ensuring the normal operation of hydraulic systems, mainly including anti-wear performance, oxidation resistance, anti-emulsification performance, etc. These properties improve the performance of hydraulic oil through different action principles.
Anti-wear performance is one of the core properties of hydraulic oil composite additives. In hydraulic systems, there is frequent friction and wear between the moving pairs of key components such as hydraulic pumps and hydraulic motors. Excessive wear will lead to reduced component accuracy, increased leakage, and even system failures. Anti-wear additives in hydraulic oil composite additives, such as sulfur-phosphorus anti-wear agents, can form a tough chemical adsorption film or reaction film on the metal surface. When friction occurs on the metal surface, this protective film can effectively isolate the metal surfaces, reduce direct contact, and thus reduce the degree of wear. For example, in high-pressure hydraulic systems, anti-wear additives can withstand high contact stress, prevent severe wear phenomena such as scratches and seizures on the metal surface, and extend the service life of components.
Oxidation resistance is crucial for the long-term use of hydraulic oil. During long-term use, hydraulic oil will come into contact with oxygen in the air and undergo oxidation reactions under the action of high temperature, metal catalysis and other factors, generating harmful substances such as organic acids, gums, and sludge. These substances will increase the viscosity and acid value of hydraulic oil, reduce its lubricating performance and fluidity, and may also block filters and corrode metal components. Antioxidant additives in hydraulic oil composite additives, such as phenolic antioxidants and amine antioxidants, can inhibit oxidation reactions by capturing free radicals and decomposing peroxides. Phenolic antioxidants can provide hydrogen atoms to free radicals, making them inactive; amine antioxidants can react with peroxides to convert them into stable compounds, thereby delaying the oxidative deterioration of hydraulic oil and extending its service life.
Anti-emulsification performance is also an indispensable property of hydraulic oil composite additives. During the operation of hydraulic systems, water can easily mix into hydraulic oil due to cooling system leakage, humid environment and other reasons. After water and hydraulic oil form an emulsion, it will destroy the lubricating film of hydraulic oil, reduce its lubricating performance, and also accelerate the corrosion of metal components. Anti-emulsification additives in hydraulic oil composite additives can reduce the tension at the oil-water interface, allowing the mixed water to quickly separate from the hydraulic oil, thereby maintaining the good lubricating performance of hydraulic oil. For example, in hydraulic systems working in humid environments, such as the hydraulic systems of mining machinery, hydraulic oil composite additives with excellent anti-emulsification performance can effectively reduce the harm of water to the system and ensure the stable operation of the system.
In order to meet the performance requirements of hydraulic oil composite additives under different working conditions, it is necessary to adopt scientific and reasonable methods and strategies for performance optimization, mainly including additive formula adjustment and base oil selection.
Additive formula adjustment is a key means to optimize the performance of hydraulic oil composite additives. Different additives have different functions, and synergistic effects can be achieved through reasonable compounding. For example, compounding anti-wear additives with extreme pressure additives can form a stronger protective film under high pressure and high temperature conditions, improving the anti-wear and extreme pressure performance of hydraulic oil. When adjusting the formula, it is necessary to consider the compatibility between additives to avoid chemical reactions between different additives that reduce performance. At the same time, the optimal proportion of additives should be determined according to specific working conditions. For hydraulic systems working in low-temperature environments, the proportion of pour point depressants needs to be increased to reduce the freezing point of hydraulic oil and ensure its fluidity at low temperatures; for hydraulic systems operating in high-temperature environments, the content of antioxidant additives should be increased to enhance their oxidation resistance. In addition, new additives can be introduced to improve the performance of composite additives. For example, nano-scale anti-wear additives, with small particle size and large specific surface area, can be more uniformly dispersed in hydraulic oil and make more sufficient contact with the metal surface, thereby further improving anti-wear performance.
The selection of base oil has an important impact on the performance of hydraulic oil composite additives. Base oil is the main component of hydraulic oil, and its properties directly determine the basic performance of hydraulic oil. Currently, commonly used base oils include mineral oils, synthetic oils, and semi-synthetic oils. Mineral oils have wide sources and low costs, but have certain limitations in high-temperature, low-temperature performance and oxidation resistance. Synthetic oils such as polyalphaolefins (PAO) have excellent high-temperature stability, low-temperature fluidity and oxidation resistance, and are suitable for hydraulic systems with high performance requirements. When selecting base oils, comprehensive consideration should be given to the working conditions and performance requirements of the hydraulic system. For hydraulic systems under normal working conditions, mineral oil can be selected as the base oil to reduce costs; for hydraulic systems operating under harsh conditions such as extreme temperatures and high pressures, synthetic oil should be selected as the base oil to ensure the excellent performance of hydraulic oil composite additives. At the same time, the compatibility between base oil and additives cannot be ignored. Only when the base oil and additives are well compatible can the additives fully play their role and achieve the optimization of the composite additive performance. For example, synthetic oils have better compatibility with certain antioxidant additives, which can more effectively exert the role of antioxidant additives and extend the service life of hydraulic oil.
With the continuous development of industrial technology, the application fields of hydraulic oil composite additives are also expanding, and many new application cases have emerged in engineering machinery, aerospace and other fields.
In the field of engineering machinery, the application of hydraulic oil composite additives has been further deepened. Traditional engineering machinery such as excavators and loaders have high requirements for the anti-wear and oxidation resistance of hydraulic oil. The application of hydraulic oil composite additives with optimized performance in these equipment can significantly reduce the failure rate of hydraulic systems and improve the working efficiency of the equipment. For example, a large engineering machinery manufacturer adopted a new type of anti-wear hydraulic oil composite additive in its new excavator, which extended the service life of the hydraulic pump by more than 30% and reduced the maintenance cost of the equipment by 20%. At the same time, with the development of new energy engineering machinery, such as electric excavators and electric cranes, new requirements are put forward for hydraulic oil composite additives. During the operation of the hydraulic system of new energy engineering machinery, due to the characteristics of motor drive, the working temperature of the hydraulic system is relatively low, but the requirements for low-temperature fluidity and electrical insulation performance of hydraulic oil are higher. In response to this demand, a special hydraulic oil composite additive has been developed, which can meet the special performance requirements of the hydraulic system of new energy engineering machinery by optimizing the additive formula and selecting appropriate base oil, providing strong support for the development of new energy engineering machinery.
In the aerospace field, the application of hydraulic oil composite additives has also made new breakthroughs. Aerospace hydraulic systems have the characteristics of high pressure, high temperature and high precision, and have extremely strict performance requirements for hydraulic oil. High-performance hydraulic oil composite additives can ensure the reliable operation of hydraulic systems under extreme working conditions. For example, in the hydraulic system of large passenger planes, the hydraulic oil composite additives used have excellent high-temperature stability and anti-wear performance, which can withstand working temperatures up to 300°C and extremely high system pressure, ensuring the precise control of key components such as the landing gear and flaps of the aircraft. In the aerospace field, the hydraulic systems of satellites and rockets need to work in extreme environments such as vacuum and low temperature. Hydraulic oil composite additives not only need to have good lubricating performance, but also have extremely low evaporation loss and excellent low-temperature fluidity. A special hydraulic oil composite additive developed by a space research institution, by using special additives and synthetic base oil, can maintain good fluidity in a low-temperature environment of -60°C, and the evaporation loss rate in a vacuum environment is less than 0.5%, meeting the harsh requirements of aerospace hydraulic systems.
To sum up, hydraulic oil composite additives play an irreplaceable important role in modern industry. Their performance optimization and application expansion are of great significance for improving the operating efficiency, reliability and safety of industrial equipment. By continuously optimizing the additive formula and reasonably selecting base oil, the anti-wear, oxidation resistance, anti-emulsification and other properties of hydraulic oil composite additives can be significantly improved, making them better adapt to different working conditions. At the same time, expanding the application of hydraulic oil composite additives to more fields such as engineering machinery and aerospace can not only meet the needs of various industries for high-performance hydraulic oil, but also promote the technological progress and development of related industries.
With the continuous innovation of industrial technology, hydraulic oil composite additives will develop towards more efficient, environmentally friendly and multi-functional directions in the future. In terms of performance optimization, more new environmentally friendly additives and advanced formula design methods will be adopted to reduce environmental pollution and further improve their comprehensive performance; in terms of application expansion, they will continuously adapt to the development needs of emerging industries, such as new energy and intelligent manufacturing, and provide customized hydraulic oil composite additive solutions for them. It can be predicted that hydraulic oil composite additives will play a more important role in the future industrial development and contribute more to the high-quality development of modern industry.
The Price of Hydraulic Oil Additives Package
The price of Hydraulic Oil Additives Package varies depending on factors such as brand, specification, composition, and sales channels. If you are interested in Hydraulic Oil Additives Package, please feel free to contact us.
Supplier of Hydraulic Oil Additives Package
UNPChemicals is a professional supplier of high-quality and effective Hydraulic Oil Additives Package. We offer several remarkable products, namely High zinc hydraulic oil additives UNP AH502A,Low Zinc Hydraulic Oil Additives UNP AH502B,Zinc-free Hydraulic Oil Additives UNP AH502C,etc.
High zinc hydraulic oil additives UNP AH502A are a type of chemical additive used in hydraulic oils that contain high levels of zinc dialkyldithiophosphate (ZDDP). ZDDP is a well-known anti-wear agent that also provides antioxidant, anti-corrosion, and anti-foam properties. The zinc in these additives plays a crucial role in forming a protective film on metal surfaces within the hydraulic system, thereby reducing wear and extending the life of the system components.
Low Zinc Hydraulic Oil Additives UNP AH502B are a class of advanced lubricant additives designed to enhance the performance of hydraulic oils with reduced zinc content.These additives are formulated to provide a balance of anti-wear,extreme pressure,and antioxidant properties,making them suitable for modern hydraulic systems that demand high performance with lower environmental impact.
Zinc-free Hydraulic Oil Additives UNP AH502C are a new class of environmentally friendly lubricant additives designed for hydraulic systems.These additives are formulated to provide the same level of performance as traditional zinc-containing additives but without the heavy metal content,reducing the environmental impact of hydraulic fluids.
Professional Lubricant Additive Manufacturer
UNPChemicals,aka Luoyang Pacific United Petrochemical Co., Ltd., focuses on the application and development of special lubricating grease additives such as MODTC, MODTP, molybdenum amide, thiadiazole metal deactivators, and phosphate esters. With nearly 30 products in seven series, including extreme pressure anti-wear additives and special grease additives, it is a global manufacturer of special lubricating grease additives and a national high-tech enterprise with great influence and leading role in the industry. If you are looking for Lubricant Additive or technical information, feel free to contact UNPChemicals.