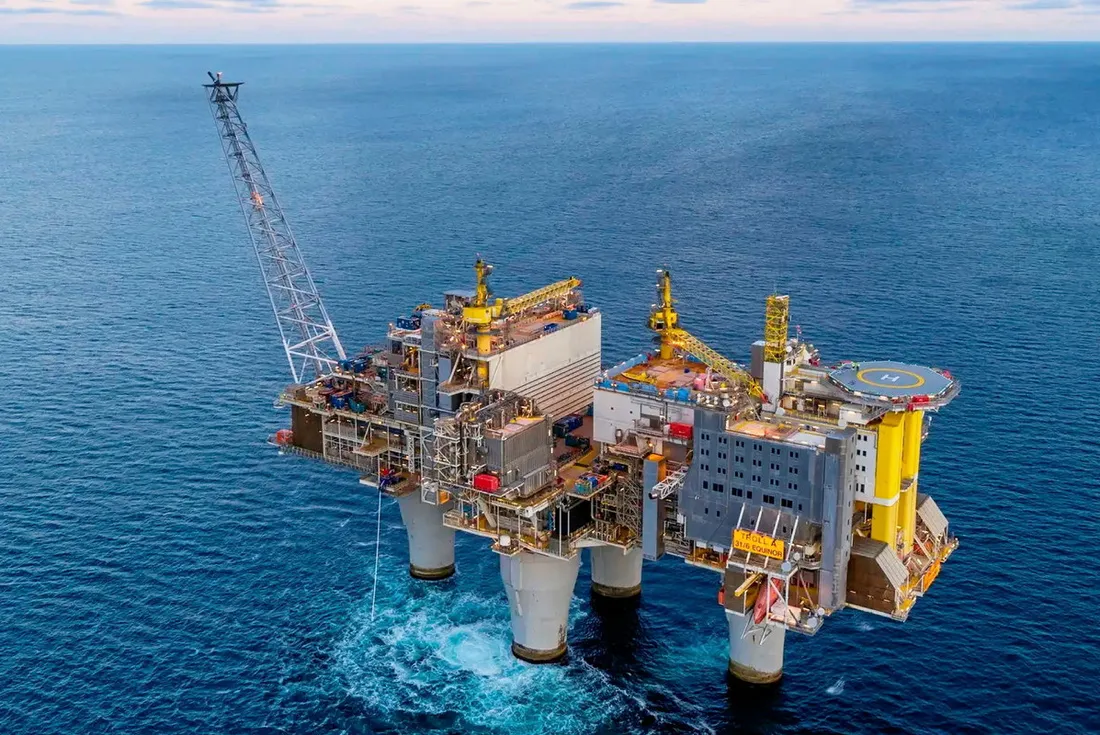
Dodecyl Dipropylene Triamine (Y12D): A Comprehensive Guide to Its Application as an Oilfield Biocide
Introduction
In the complex ecosystem of oilfield operations, microbial contamination presents one of the most persistent and costly challenges facing the industry today. The proliferation of sulfate-reducing bacteria (SRB), acid-producing bacteria (APB), and other microorganisms in oilfield systems leads to a cascade of operational problems including microbiologically influenced corrosion (MIC), reservoir souring, and biofilm-related flow assurance issues. These microbial activities are estimated to cost the global oil and gas industry billions annually in lost production, equipment damage, and remediation efforts.
Among the various strategies employed to combat microbial contamination, the use of specialized biocides remains the most direct and effective approach. In this context, Dodecyl Dipropylene Triamine (Y12D) has emerged as a particularly effective solution, combining broad-spectrum antimicrobial activity with excellent system compatibility and favorable environmental characteristics. This white paper provides a comprehensive technical review of Y12D as an oilfield biocide, examining its chemical properties, mechanism of action, field applications, and economic considerations.
The discussion is structured to address four key areas:
Fundamentals of oilfield biocides - Understanding the microbial threats and biocide requirements in petroleum operations
Chemical profile of Y12D - Detailed examination of its molecular structure and functional properties
Operational applications - Field-proven implementation strategies across various oilfield systems
Economic analysis - Cost considerations and procurement strategies for optimal deployment
This document is intended to serve as a technical reference for production chemists, microbiologists, facility engineers, and procurement specialists involved in oilfield microbial control programs. The information presented is based on peer-reviewed research, field trial data, and industry best practices current as of 2024.
1. Oilfield Biocides: Critical Components in Microbial Management
1.1 The Microbial Ecology of Oilfield Systems
Oilfield environments provide ideal conditions for diverse microbial communities due to:
Anaerobic conditions in reservoirs and pipelines
Availability of organic carbon sources
Moderate temperatures in most production systems
Presence of sulfate in formation and injection waters
The primary microbial threats in oilfield systems include:
1.1.1 Sulfate-Reducing Bacteria (SRB)
Convert sulfate to hydrogen sulfide (H₂S)
Primary contributors to MIC and reservoir souring
Examples: Desulfovibrio, Desulfotomaculum species
Cause pitting corrosion rates up to 1-5 mm/year
1.1.2 Acid-Producing Bacteria (APB)
Generate organic acids that lower pH
Accelerate general corrosion
Examples: Clostridium, Acetobacterium species
1.1.3 Methanogens
Produce methane in reservoirs
Can contribute to corrosion through cathodic depolarization
Examples: Methanobacterium, Methanococcus species
1.1.4 Biofilm-Forming Bacteria
Create protective extracellular polymeric substances (EPS)
Lead to under-deposit corrosion
Examples: Pseudomonas, Bacillus species
Table 1.1: Microbial Populations in Typical Oilfield Water Systems
1.2 Mechanisms of Microbial Damage in Oilfield Systems
1.2.1 Microbiologically Influenced Corrosion (MIC)
Electrochemical corrosion enhanced by microbial activity
SRB catalyze cathodic depolarization
Biofilms create concentration cells
Estimated to account for 20-30% of all corrosion costs
1.2.2 Reservoir Souring
H₂S generation in reservoirs
Decreases hydrocarbon value
Creates safety hazards
Requires additional processing
1.2.3 Biofouling and Flow Assurance Issues
Biofilm accumulation reduces pipe diameter
Increases pumping pressure
Interferes with separation processes
Promutes under-deposit corrosion
1.3 Biocide Requirements for Oilfield Applications
Effective oilfield biocides must meet stringent performance criteria:
Table 1.2: Key Performance Requirements for Oilfield Biocides
2. Dodecyl Dipropylene Triamine (Y12D): Chemical Profile and Properties
2.1 Molecular Structure and Synthesis
Y12D is a polyamine compound with the systematic IUPAC name:
N-Dodecyl-N'-(3-aminopropyl)-1,3-propanediamine
Chemical Structure:
CH₃(CH₂)₁₁
|
NH₂-(CH₂)₃-NH-(CH₂)₃-NH₂
Synthesis Pathway:
Alkylation Step:
Dodecylamine + Acrylonitrile → DodecylaminopropionitrileHydrogenation Step:
Dodecylaminopropionitrile + H₂ → DodecylaminopropylamineSecond Alkylation:
Dodecylaminopropylamine + Acrylonitrile → Intermediate nitrileFinal Hydrogenation:
Intermediate nitrile + H₂ → Y12D final product
2.2 Physicochemical Properties
Table 2.1: Key Physicochemical Properties of Y12D
2.3 Antimicrobial Mechanism of Action
Y12D exhibits a multi-modal antimicrobial mechanism:
2.3.1 Cell Membrane Disruption
Cationic amine groups interact with negatively charged cell membranes
Hydrophobic dodecyl chain penetrates lipid bilayer
Causes loss of membrane integrity and cell lysis
2.3.2 Intracellular Effects
Penetrates cytoplasm and binds to nucleic acids
Inhibits key enzymes in energy metabolism
Disrupts protein synthesis pathways
2.3.3 Biofilm Penetration and Disruption
Cationic nature facilitates EPS penetration
Disperses existing biofilms
Prevents new biofilm formation
2.4 Performance Advantages Over Conventional Biocides
Table 2.2: Comparative Performance of Y12D vs. Common Oilfield Biocides
3. Field Applications and Implementation Strategies
3.1 Produced Water Treatment
3.1.1 Continuous Injection Programs
Typical dosage: 50-150 ppm
Injection points:
Downstream of separators
Before water holding tanks
At injection pump suction
3.1.2 Batch Treatment Programs
Shock dose concentration: 200-500 ppm
Contact time: 4-24 hours
Frequency: Weekly to monthly based on monitoring
Case Study: Offshore Production Platform
Problem: SRB counts >10⁵ cells/mL in produced water
Solution: Y12D at 100 ppm continuous + 300 ppm monthly batch
Results:
SRB reduced to <10² cells/mL
H₂S levels decreased by 85%
Corrosion rate reduced from 0.8 to 0.1 mm/yr
3.2 Pipeline Biofilm Control
3.2.1 Pigging-Assisted Treatment
Pre-pig flush with Y12D solution (200-400 ppm)
Mechanical cleaning followed by biocide soak
Effective for pipelines up to 24" diameter
3.2.2 Squeeze Treatment
For unpiggable lines
Soak volume calculation: 1.5-2× pipe volume
Contact time: 24-48 hours
3.3 Hydraulic Fracturing Applications
3.3.1 Fracturing Fluid Preservation
Dosage: 100-200 ppm in frac water
Prevents microbial degradation of polymers
Maintains fluid viscosity
3.3.2 Flowback Water Treatment
Controls SRB during flowback
Prevents downhole contamination
3.4 Reservoir Souring Mitigation
3.4.1 Injection Water Treatment
Continuous injection at 50-100 ppm
Penetrates near-wellbore region
Inhibits SRB activity in formation
3.4.2 Matrix Squeeze Treatments
High concentration slugs (500-1000 ppm)
Extended release formulations
3-6 month treatment longevity
3.5 Monitoring and Performance Validation
3.5.1 Microbial Monitoring Techniques
ATP bioluminescence
qPCR for specific organisms
Culture methods (MPN)
3.5.2 Corrosion Monitoring
Coupon analysis
ER probes
LPR measurements
4. Economic Considerations and Procurement Strategies
4.1 Cost Structure Analysis
4.1.1 Raw Material Cost Drivers
Dodecylamine market price fluctuations
Hydrogenation process costs
Purification requirements
4.1.2 Formulation Options
Neat product vs. formulated blends
Solvent systems (aqueous vs. glycol-based)
Additive packages
4.2 2024 Market Pricing
Table 4.1: Y12D Price Ranges by Region and Purity
4.3 Total Cost of Ownership Analysis
4.3.1 Treatment Cost Calculation Example
System volume: 10,000 bbl water/day
Dosage: 100 ppm
Daily requirement: 42 kg
Annual cost at 12/kg:184,000
4.3.2 Cost-Benefit Considerations
Reduced corrosion maintenance
Extended equipment life
Improved hydrocarbon quality
Lower HSE risks
4.4 Procurement Best Practices
4.4.1 Supplier Qualification
Manufacturing capability audits
Quality control documentation
Regulatory compliance verification
4.4.2 Inventory Management
Just-in-time delivery strategies
Bulk storage considerations
Shelf-life monitoring
Conclusion and Future Outlook
Dodecyl Dipropylene Triamine (Y12D) represents a technically advanced and economically viable solution for comprehensive microbial control in oilfield systems. Its unique chemical structure provides multiple advantages over conventional biocides, particularly in challenging applications requiring biofilm penetration and thermal stability.
The future development of Y12D technology is expected to focus on:
Enhanced formulation technologies for extended release
Synergistic combinations with other treatment chemicals
Improved environmental profile through molecular modification
Smart delivery systems responsive to microbial activity
For optimal implementation, operators should:
Conduct thorough system assessments
Develop customized treatment programs
Implement robust monitoring protocols
Regularly evaluate treatment economics
As the oil and gas industry continues to face increasing challenges from microbial contamination, advanced solutions like Y12D will play an increasingly critical role in maintaining asset integrity and operational efficiency.
Dodecyl Dipropylene Triamine (Y12D) Supplier
UNPChemicals is a professional oilfield chemical manufacturer, with products covering drilling, completion, oil production, gathering and transportation, etc., and has won the trust of customers with advanced technology, strict quality control and high-quality services. We are committed to personalized solutions to help oilfields develop efficiently.