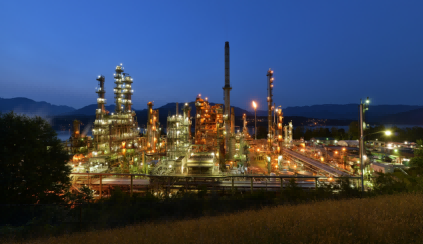
The Magic of Demulsifiers: Unlocking Oil-Water Separation
1. What is a Demulsifier?
2. The Demulsification Mechanism
- Surface Activity: Demulsifiers possess high surface activity, allowing them to quickly migrate to the oil-water interface. Once there, they replace or neutralize the natural emulsifiers that stabilize the emulsion, reducing the interfacial tension and weakening the protective film around water droplets. This action makes it easier for the water droplets to coalesce and separate from the oil phase.
- Phase Inversion: Some demulsifiers can induce a phase inversion, transforming a water-in-oil (W/O) emulsion into an oil-in-water (O/W) emulsion. This change in structure destabilizes the emulsion, making it easier for water droplets to coalesce and separate. Phase inversion is particularly useful in treating heavy oils, where the emulsion stability is often higher due to the presence of more complex and viscous components.
- Collision and Disruption: Under conditions of heating or agitation, demulsifiers collide with the interfacial films of the emulsion. They can either adsorb onto these films or displace part of the surface-active substances, thereby disrupting the film and causing the emulsion to break down. This mechanical action is often enhanced by the presence of heat, which reduces the viscosity of the oil and allows for more efficient mixing and interaction between the demulsifier and the emulsion.
- Electrostatic Neutralization: In cases where the emulsion droplets carry an electric charge, demulsifiers can neutralize this charge, reducing the repulsive forces between droplets and promoting their coalescence. This mechanism is particularly effective in treating emulsions formed in the presence of electrolytes, where the charge stabilization of droplets can significantly hinder separation.
- Coalescence Promotion: Demulsifiers can also promote the coalescence of water droplets by reducing the interfacial tension between them. Once the droplets come into contact, the demulsifier helps in merging them into larger droplets, which then separate more easily from the oil phase due to differences in density. This process is often accelerated by the use of coalescing aids, such as mesh screens or packed columns, which provide a surface for droplet coalescence.
3. Classification of Demulsifiers
- Cationic Demulsifiers: These are positively charged and include compounds like quaternary ammonium salts. They are effective for light oils but may not perform well with heavy or aged oils. Cationic demulsifiers work by neutralizing the negative charges on the surface of water droplets, reducing repulsive forces and promoting coalescence. However, their effectiveness can be limited in the presence of high concentrations of salts or other electrolytes, which can interfere with their charge neutralization mechanism.
- Anionic Demulsifiers: These carry a negative charge and include carboxylates, sulfonates, and sulfate esters. They are generally less effective due to their sensitivity to electrolytes and higher dosage requirements. Anionic demulsifiers are more commonly used in applications where the emulsion stability is primarily due to the presence of positively charged components. However, their performance can be significantly affected by the presence of multivalent cations, which can form insoluble salts with the anionic groups, reducing their effectiveness.
- Nonionic Demulsifiers: These are neutral and include polyether-based compounds such as polyoxyethylene and polyoxypropylene derivatives. They are versatile and can be tailored for specific applications, including those involving heavy oils. Nonionic demulsifiers are less sensitive to the presence of salts and electrolytes, making them suitable for a wide range of applications. Their effectiveness is primarily due to their ability to reduce interfacial tension and promote coalescence without relying on charge neutralization.
- Amphoteric Demulsifiers: These can exhibit both positive and negative charges under different conditions. They are useful for complex emulsions and can offer enhanced performance in specific scenarios. Amphoteric demulsifiers can adapt to varying pH conditions and can neutralize both positive and negative charges on the emulsion droplets, making them highly effective in treating complex emulsions formed in diverse industrial processes.
4. Applications of Demulsifiers
(1)Electrodesalting
- Mechanism: Demulsifiers reduce the interfacial tension between oil and water, allowing the water droplets to coalesce and separate more easily. This ensures that the salts, which are dissolved in the water phase, can be removed efficiently.
- Benefits: By effectively breaking the emulsions, demulsifiers enhance the efficiency of the electrodesalting process, reducing the salt content to acceptable levels and minimizing the risk of corrosion and fouling in downstream units.
- Optimization: The selection of the appropriate demulsifier is crucial, as different crude oils have varying compositions and emulsion stabilities. Demulsifiers are often tailored to match the specific characteristics of the crude oil being processed.
(2) Water-in-Oil Demulsification
- Mechanism: Demulsifiers penetrate the interfacial film of the emulsion, neutralizing the stabilizing agents and reducing the interfacial tension. This allows the water droplets to coalesce and separate from the oil phase.
- Benefits: Efficient demulsification reduces the water content in crude oil, improving its quality and reducing transportation costs. It also prevents operational issues such as pipeline corrosion and blockages.
- Application: Demulsifiers are typically added at the production site or during transportation, ensuring that the crude oil meets the required specifications before entering the refinery.
(3)Drying Agents
- Mechanism: Demulsifiers destabilize the water droplets dispersed in the oil, promoting their coalescence and separation. This is particularly important in processes such as distillation, where the presence of water can affect the efficiency of the separation.
- Benefits: By removing water, demulsifiers prevent operational issues such as flooding in distillation columns and improve the overall efficiency of the refining process.
- Application: Demulsifiers are used in various stages of the refining process, including pre-treatment of crude oil, intermediate product drying, and final product polishing.
(4)Rapid Dehydration
- Mechanism: Demulsifiers quickly migrate to the oil-water interface, disrupting the emulsion stability and promoting rapid water separation. This is particularly useful in situations where quick turnaround is necessary, such as in mobile oil processing units or emergency response scenarios.
- Benefits: Rapid dehydration reduces the time and energy required for water removal, improving operational efficiency and reducing costs. It also minimizes the risk of water-related issues in downstream processing.
- Application: Demulsifiers are used in rapid dehydration units, often in combination with heating and agitation to enhance the separation process. They are also used in emergency response situations where quick removal of water is necessary to prevent operational disruptions.
5. Pricing of Demulsifiers
- Chemical Composition: The type of demulsifier (e.g., cationic, anionic, nonionic) and its specific formulation can significantly impact pricing. For example, nonionic demulsifiers, which are often more complex and versatile, may be priced higher than simpler anionic or cationic types. The cost of raw materials used in the synthesis of demulsifiers also plays a crucial role in determining their final price. For instance, polyether-based nonionic demulsifiers may be more expensive due to the higher cost of their precursor compounds.
- Application-Specific Formulations: Customized demulsifiers designed for specific industrial processes or environmental conditions can command higher prices due to their specialized nature. These formulations often involve extensive research and development to ensure optimal performance in challenging conditions. For example, demulsifiers designed for heavy oil applications may require higher concentrations of active ingredients and more complex formulations to effectively break down the stable emulsions formed in such environments.
- Market Supply and Demand: The availability of raw materials and the overall market demand for demulsifiers also influence pricing. In regions with high oil production or significant industrial wastewater treatment needs, demand can drive up prices. Additionally, fluctuations in the prices of raw materials, such as petroleum-based compounds or specialty chemicals, can impact the cost of demulsifiers. In times of high demand or limited supply, prices may rise, reflecting the market conditions.
- Regulatory Requirements: In some industries, particularly those involving environmental protection or food processing, demulsifiers may need to meet specific regulatory standards. These requirements can add to the cost of production, as manufacturers may need to invest in additional testing and certification processes to ensure compliance. For example, demulsifiers used in food and beverage applications must meet stringent food safety regulations, which can increase their cost compared to those used in non-food industries.
In summary, demulsifiers are essential tools in various industries, offering efficient solutions for oil-water separation. Their effectiveness and versatility make them indispensable, despite the varying costs associated with different types and applications. By understanding the principles of demulsification, the classification of demulsifiers, and the factors influencing their pricing, industries can make informed decisions to optimize their processes and improve operational efficiency.
Demulsifiers Supplier
UNPChemicals is a professional oilfield chemical manufacturer, with products covering drilling, completion, oil production, gathering and transportation, etc., and has won the trust of customers with advanced technology, strict quality control and high-quality services. We are committed to personalized solutions to help oilfields develop efficiently.
UNPChemicals' Demulsifiers
DEMETâ„¢ A-21 demulsifier is a liquid oxyalkylate category, utilized in the industrial market for crude oil desalting processes, particularly in exploration and upstream applications.
DEMETâ„¢ C-232 demulsifier is a resin oxyalkylate intermediate utilized predominantly as a Water Dropper in oilfield production. It is also occasionally employed as a Dryer and an Interface Control Agent. It is effective for a broad spectrum of API crudes globally, including those in low-temperature scenarios.
DEMETâ„¢ C-168 demulsifier, a resin oxyalkylate intermediate, is primarily utilized in oilfield production as a Water Dropper, and also serves as a Dryer and Interface Control Agent for a broad spectrum of API crudes worldwide, including those in low-temperature environments.