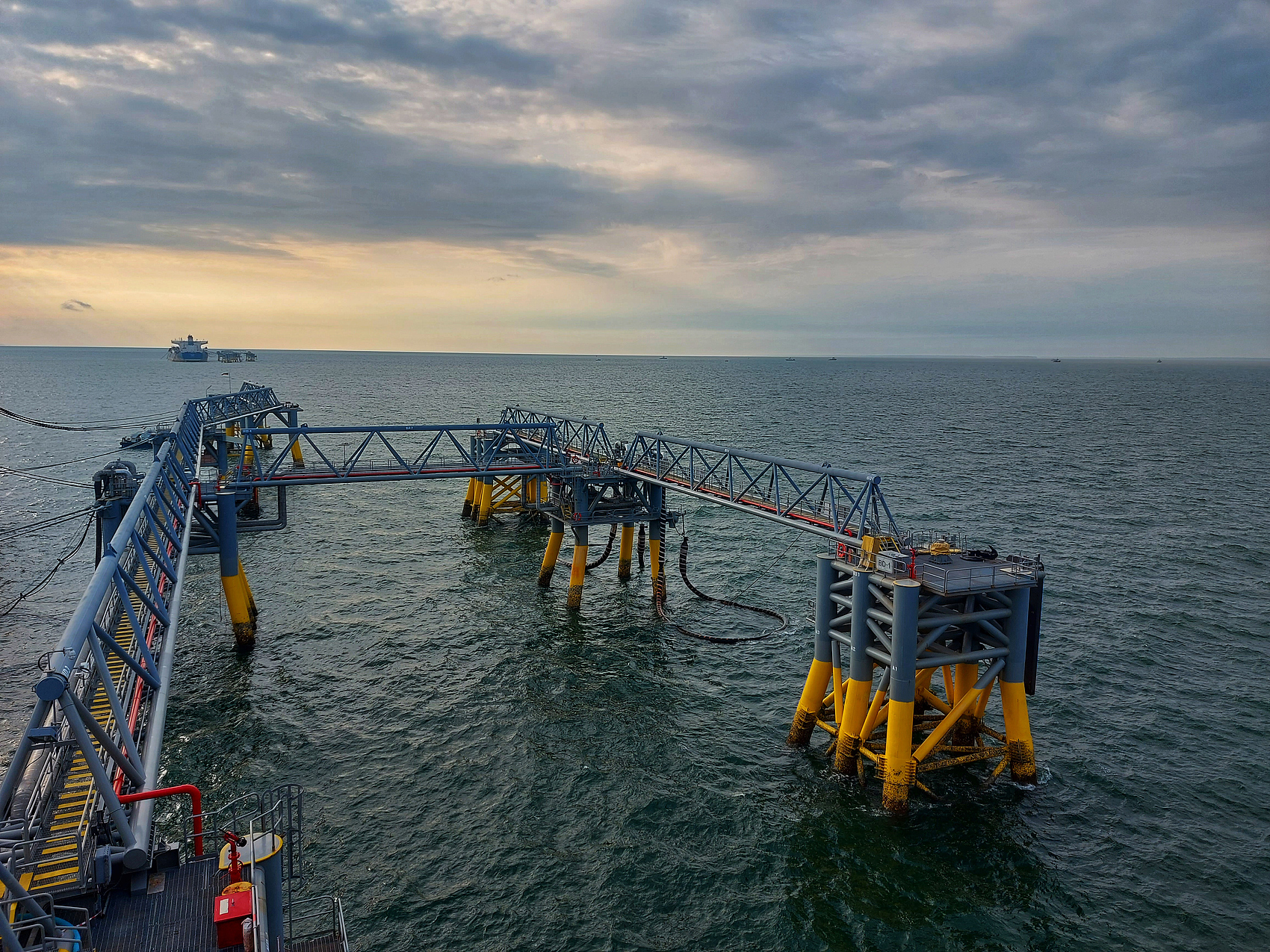
Advanced Corrosion Inhibitors in Oilfield Applications: Mechanisms, Innovations, and Economic Considerations
1. The Science of Oilfield Corrosion: Why Inhibitors Are Essential
Corrosion in oilfield operations represents a complex electrochemical phenomenon that manifests differently across various production systems. The fundamental corrosion process begins when metal surfaces interact with aqueous environments containing dissolved gases (CO₂, H₂S, O₂), forming galvanic cells that drive oxidation-reduction reactions. In sweet corrosion (CO₂-dominated), carbonic acid formation lowers pH to 3-4, accelerating metal dissolution rates up to 15 mm/year. Sour corrosion (H₂S presence) is particularly insidious, as iron sulfide scales often form non-protective porous layers, while hydrogen embrittlement can lead to catastrophic failure.
Microbiologically influenced corrosion (MIC) adds another dimension, with sulfate-reducing bacteria (SRB) producing corrosive hydrogen sulfide locally at concentrations up to 1000 ppm beneath biofilms. Recent studies show that MIC accounts for 20-30% of all corrosion failures in water injection systems. The economic impact is staggering - a single offshore platform may incur over 50 million annually in corrosion-related maintenance, while pipeline replacements can exceed
1 million per mile.
Modern corrosion inhibitors counteract these mechanisms through sophisticated molecular design. UNP-CIMET imidazoline derivatives, for instance, employ a dual-function mechanism: the polar amine group chemisorbs to metal surfaces with binding energies of 40-60 kJ/mol, while the hydrophobic C17 alkyl chain forms a dense monolayer with surface coverage exceeding 90% at concentrations as low as 25 ppm. Advanced formulations like UNP-550 incorporate phosphate esters that synergize with imidazolines, reducing critical micelle concentration (CMC) by 30% and improving temperature stability to 175°C.
2. Comprehensive Classification of Oilfield Corrosion Inhibitors
The chemical diversity of modern corrosion inhibitors reflects the varied challenges across oilfield environments. Nitrogen-based inhibitors dominate the market, with imidazolines representing approximately 45% of all formulations. UNP-CIMET's molecular architecture features a 17-carbon hydrophobic tail (derived from oleic acid) and an imidazoline ring that protonates in acidic conditions, creating a positively charged adsorption center. This structure provides 98.7% inhibition efficiency in CO₂-saturated brine at 80°C, as demonstrated by rotating cylinder electrode tests per ASTM G185.
Phosphorus-containing inhibitors have evolved significantly from early phosphate esters. Contemporary phosphonates like HEDP (hydroxyethylidene diphosphonic acid) exhibit exceptional scale inhibition properties while providing supplemental corrosion protection. UNP's patented UNP-425 series combines quaternary ammonium groups with phosphonate functionality, achieving 99.2% efficiency against both corrosion and scale in high-TDS (total dissolved solids) brines exceeding 200,000 ppm.
The emerging category of nano-enhanced inhibitors represents a paradigm shift. UNP formulations incorporate graphene oxide nanosheets (0.5-2 wt%) that provide barrier protection through extraordinary aspect ratios (>1000:1). Laboratory data shows these materials reduce corrosion current density (icorr) from 12.5 µA/cm² to 0.3 µA/cm² in H₂S environments, while field trials in the Permian Basin demonstrated a 70% reduction in inhibitor dosage requirements compared to conventional products.
3. Advanced Application Methodologies
Effective corrosion management requires precise deployment strategies tailored to system characteristics. Continuous injection systems demand careful flow modeling to ensure proper inhibitor distribution. In multiphase pipelines, computational fluid dynamics (CFD) simulations reveal that injection points should be located at least 50 pipe diameters upstream of critical sections to achieve >90% wall coverage. UNP's SmartDose technology uses real-time monitoring of residual inhibitor concentrations (via HPLC analysis) to maintain optimal treatment levels between 25-150 ppm.
Batch treatment protocols have advanced significantly with the development of viscous inhibitor pills. UNP's GelTec formulations exhibit thixotropic behavior, with viscosity decreasing from 10,000 cP during static conditions to 200 cP under shear, ensuring complete pipeline coverage during pigging operations. Field data from the North Sea shows these pills can maintain protective films for up to 6 months in 24-inch export pipelines.
For downhole applications, UNP has pioneered microencapsulated inhibitors (UNP-CIMET series) with pH-sensitive release mechanisms. The polyurethane shell remains intact at neutral pH but degrades rapidly in acidic environments (pH<4), targeting inhibitor release precisely where CO₂ corrosion initiates. This technology has reduced chemical consumption by 40% in acid gas injection wells while maintaining corrosion rates below 0.1 mm/year.
4. Performance Optimization and Case Studies
The Eagle Ford shale presents unique corrosion challenges due to high bottomhole temperatures (150-175°C) and variable H₂S concentrations (50-500 ppm). UNP's thermal-stable inhibitor UNP-HT800, incorporating rare earth metal synergists, demonstrated 99.1% efficiency in autoclave tests at 175°C/5000 psi, compared to 87.5% for conventional imidazolines. Field implementation reduced workover frequency from biannual to quadrennial, generating an estimated $4.2 million NPV per well over 5 years.
Offshore Brazil's pre-salt fields require inhibitors compatible with high-salinity brines (300,000+ ppm TDS) and CO₂ partial pressures exceeding 1000 psi. UNP's polymeric inhibitor UNP-850 maintains performance where traditional products fail, forming stable protective films even at shear stresses >100 Pa. After implementation across 22 subsea wells, corrosion-related failures decreased from 3.2 incidents/year to zero over a 36-month observation period.
Economic analysis reveals compelling ROI across applications. A Gulf of Mexico platform implementing UNP's integrated corrosion management program (combining UNP-301 inhibitor with real-time monitoring) reduced chemical costs by 30% while extending pipeline service life from 12 to 18 years, representing a $75 million lifecycle cost reduction for the asset.
5. Economic and Environmental Considerations
The global corrosion inhibitor market exhibits complex regional dynamics. Middle Eastern operators prioritize cost efficiency in sweet corrosion applications, with bulk imidazoline purchases at 2,600-
2,900/ton. North American shale operators favor high-performance formulations, paying premiums of 20-30% for customized products like UNP's shale gas inhibitors. Asia-Pacific markets show strongest growth (7.2% CAGR), particularly for environmentally acceptable products meeting China's GB 30000-2013 standards.
Environmental regulations are reshaping formulation strategies. The 2024 update to OSPAR Recommendation 2012/5 imposes strict limits on organic compound persistence, prompting development of UNP EcoShield inhibitors featuring ester-based chemistry with 28-day biodegradation >60%. These products now command 15% market share in the North Sea, despite 25-40% price premiums over conventional inhibitors.
Lifecycle cost analysis demonstrates that advanced inhibitors often prove most economical. While nano-enhanced CIMET costs 8,500/ton versus
3,200 for standard imidazolines, its 70% dosage reduction and extended treatment intervals yield 18-24 month payback periods in most applications. Digital dosing systems can improve this further - Shell's Machine Learning Optimizer (MLO) system achieved 22% chemical savings across 150 wells using UNP inhibitors.
6. Future Directions and Emerging Technologies
Metallic-organic frameworks (MOFs) represent perhaps the most promising frontier. UNP's research with ZIF-8 (zeolitic imidazolate framework) demonstrates unprecedented inhibitor loading capacities of 1.2 g inhibitor/g MOF, with pH-triggered release kinetics. Field trials in Alberta's sour gas fields show these materials maintain protection for 9-12 months between treatments, compared to 3-4 months for conventional products.
Self-healing coatings incorporating microencapsulated inhibitors (UNP-CIMET series) are revolutionizing surface protection. When scratches occur, the capsules rupture, releasing healing agents that polymerize in situ. Testing per ISO 12944-9 shows these coatings maintain >95% protection after 5,000 hours of salt spray exposure, even with 2mm artificial defects.
Digital twin technology is transforming corrosion management. UNP's CorrOptix system integrates computational fluid dynamics, electrochemical monitoring, and machine learning to predict corrosion hot spots with 92% accuracy. Pilot implementations have reduced unplanned shutdowns by 40% while optimizing chemical usage within 5% of theoretical minimums.
The coming decade will likely see commercialization of bioelectronic inhibitors - molecules that can switch between active and passive states in response to electrical signals, potentially enabling real-time corrosion control adjustments without chemical dosage changes. UNP's patent filings suggest such technologies may reach field trials by 2027.
Corrosion Inhibitors Supplier
UNPChemicals is a professional oilfield chemical manufacturer, with products covering drilling, completion, oil production, gathering and transportation, etc., and has won the trust of customers with advanced technology, strict quality control and high-quality services. We are committed to personalized solutions to help oilfields develop efficiently.