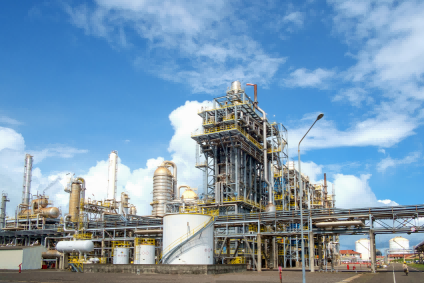
Application of Demulsifier in Oil and Gas Gathering and Transportation System
Crude oil demulsifier is a widely used chemical additive in oilfields. It mainly penetrates into and adheres to the interface of emulsified droplets, replaces the original emulsifier and destroys the surface film, releases the droplets coated in the film and makes them coalesce, and separates the oil phase from the water phase through the influence of gravity. Demulsifiers are usually used in oilfield oil transfer and water discharge stations and joint stations, and the addition point is generally the integrated liquid between the valve groups. However, the processing time of the oil and gas gathering and transportation sytem of the joint station is relatively long, and the indicators for the external transmission of crude oil and sewage are very high. Therefore, some joint stations will set up one to two or even more demulsifier agent addition points. In order to ensure the stable operation of the entire oil and gas gathering and transportation system, different types of agents are sometimes added simultaneously at multiple agent addition points.
1 Effect of demulsifier
The oil and water in the oil field formation are layered, and the two will not produce emulsions due to the influence of density. However, in the process of oil recovery, due to the application of oil displacement technology, the oil phase and the water phase form a mixture. In the process of flowing along the oil pipe, the associated gas in the mixture is precipitated due to the pressure, thus indirectly stirring the oil-water mixture. In addition, the use of equipment such as dewatering pumps and centrifugal pump fittings in the oil and gas gathering and transportation process promotes the formation of emulsions.
Another reason for the easy formation of emulsions is that the natural emulsifier components contained in crude oil, such as asphaltene, colloid, wax and other organic matter, form a lot of emulsions with smaller internal phase particles and higher dispersion during the long migration time in the oil recovery process. The smaller and more dispersed the water droplets are, the smaller the gravity they are subjected to, and it is less likely to settle. At the same time, the high molecular organic matter in crude oil itself also helps to form an interfacial film with high viscosity and elasticity. This interfacial film with high mechanical strength will further enhance the stability of the emulsion. This is also the main reason for the easy generation of W/O emulsions, making this type of medium appear to be much more lipophilic than hydrophilic. Therefore, in order to make the water content of crude oil meet the standards and better refine finished oil and related products, the produced fluid needs to be deeply demulsified.
2 Application of demulsifiers in oilfield transfer stations
The oil-water separation equipment in oilfield transfer stations is mostly a three-in-one separator for oil, gas and water three-phase separation. The separated water is used for wellhead heating back mixing or external transmission to downstream sewage treatment stations. The incoming liquid that has not been added with demulsifiers can only be separated by the difference in oil and water density. The oil-water separation effect is poor and the separation time is long, which often causes the oil content of the back mixing water or external sewage to exceed the standard, which not only reduces the crude oil production, but also causes great difficulties for downstream sewage treatment. After adding demulsifiers, the oil-water separation speed can be increased, and the water quality of the demulsified sewage can be indirectly improved. While ensuring the crude oil production, it reduces the treatment burden of the downstream sewage station. It can be seen that the application of demulsifiers in transfer stations plays a very important role. By improving the ability of oil-water separation to reduce the treatment difficulty of the downstream station, it also reduces the treatment burden of the sewage system of this station, thereby extending the filter tank cleaning cycle of the oil production plant and saving operating costs for the oil production plant.
With the application of new oilfield exploitation technologies in recent years, such as ordinary polymer flooding, salt-resistant polymer flooding, ternary flooding and other technologies, the properties of oil well produced fluids have changed greatly. For example, the use of salt-resistant polymer zone oil displacement agents makes the displacement fluid have strong temperature and salt resistance, good adsorption resistance, and greatly improves the viscosity retention rate of polymers in the formation. The resulting impact is that the properties of the produced fluid have changed, making the oil-water separation effect of the transfer station and the joint station worse, and the separation of produced fluids difficult, increasing the sedimentation time on site and the oil content of the separated wastewater is high. At this time, it is necessary to select special demulsifier formulas for different media to achieve the desired effect. Taking the 115th Polyzhong Station of the First Mine of the First Oil Production Plant of Daqing Oilfield as an example, the use of salt-resistant polymers can effectively reduce the mass concentration of polymers and improve the viscosity retention rate of polymers. This also increased the difficulty of later sewage treatment. The block invested in salt-resistant polymers (models HLX12 million, HLX16 million) in August 2016 and entered the displacement stage in March 2017. Polyzhong 115 Station had been using conventional water-soluble demulsifiers before May 2017. As the use of salt-resistant polymers on site made oil-water separation more and more difficult, the oil content of external sewage remained high at 700~1000mg/L. The polymer concentration of external water on site was about 500mg/L, and the viscosity was 4.5. Through the on-site agent formula adjustment experiment for nearly four months, the difference in the effects of different agents was explored. Table 1 shows the test data tracking for four consecutive months on site.
According to the average value of the data during the use of different agent models, the on-site use effect of LS-115A demulsifier is good, and the oil content of the external wastewater has reached below 500mg/L from July 14 to July 20, basically meeting the oil content index of wastewater after separation and sedimentation required on site.
Although the oilfield transfer station does not have high requirements for the water content index of the external crude oil, the separated wastewater has a great impact on the entire oil and gas gathering and transportation system. The mixed wastewater directly affects the difficulty of processing the wellhead produced fluid; the quality of the external wastewater directly affects the subsequent sewage station treatment capacity. It can be seen that the application of demulsifiers in oilfield transfer stations is also very important.
3 Application of demulsifiers in oilfield joint stations
As the production base of finished oil and gas in oilfields, joint stations have relatively complete production processes. Demulsifiers are mainly used for the addition of oilfield additives. Some joint stations also have points for adding sulfide removers, water purification viscosity reducers, water purification agents and other agents. Most transfer stations have already added demulsifiers. Therefore, the water content of the comprehensive liquid of the joint station is generally above 95%, but the water content in the emulsified oil is generally around 10%. Further chemical treatment combined with sedimentation process is required, and finally 9.7%~9.8% of water is removed under the action of the electric field of the electric dehydrator.
3.1 Selection of demulsifier types for joint stations
Since the integrated incoming liquid of the joint station already contains a lot of water, it is actually difficult to achieve a good demulsification effect by adding ordinary water-soluble agents for treatment of this part of the medium that has been treated with chemicals. In some cases, it may even appear that the amount of the agent added is too large and emulsification occurs, which increases the difficulty of oil-water separation. This part of the medium is generally divided into two categories, one is W)O type emulsified oil, and the other is O/W type free water. Therefore, when adding chemicals between the integrated incoming liquid valve groups of the joint station, chemicals that focus on these two aspects of performance should be selected for addition. Only by selecting the agent addition in a targeted manner can the burden of subsequent medium treatment be reduced.
3.1.1 Selection of reverse type agents
Whether to choose a forward or reverse demulsifier depends on the actual production situation on site. If the operation of the second-stage electric dehydrator of the joint station is relatively stable and the water content after dehydration can meet the standard of crude oil for external transportation, then for this type of medium, a reverse type demulsifier can be selected, focusing on sewage treatment, leaving the task of treating emulsified oil to the electric dehydrator, and controlling the sewage index to the best through the combined effect of agent addition and free water remover. Usually, through agent addition, the oil content of the general polymer drive medium after sedimentation in the free water remover can generally reach less than 500mg/L, and some can be less than 300mg/L, so that the whole set of oil and gas gathering and transportation system will run more smoothly.
3.1.2 Selection of positive agents
Another situation is that the electric dehydrator of the joint station is relatively fragile, and the operation often fluctuates and reverses the electric field, drains water and runs oil, and the collapse is difficult to recover. The main reason for this situation is that the emulsified oil has strong conductivity. In the process of oil field production, a more troublesome situation is often encountered, that is, there are operation and measure wells in front, or the front sewage station collects oil. Because this part of the oil is not good in nature, it contains a large amount of fine impurities that are not easy to settle and agglomerate in the oil-water transition layer, making the oil-water interface unclear. The use of various chemical oil-increasing measures makes the components of the aged oil more complex, and it is impossible to directly settle the water content to meet the standard emulsification degree. It is often transported to the joint station through the transfer station for comprehensive treatment, which increases the difficulty of the treatment of the joint station.
In this case, the treatment focus of the medium should be placed on breaking the deep emulsification. The agent is added through the joint station agent addition point, and the mechanical impurities in the emulsified oil are separated through the sedimentation tank to break the emulsified layer on the surface of the emulsified droplets, so that the small crude oil droplets are condensed into large oil droplets and input into the subsequent electric dehydrator. If this step does not achieve the expected treatment effect, this part of the medium with more serious emulsification will carry a large amount of mechanical impurities and enter the electric dehydrator, causing violent fluctuations in the electric field, making it impossible to establish a high-voltage electric field, so that the emulsified water in the emulsified oil cannot be removed, resulting in the production of high-water crude oil for external transmission. Through years of indoor experiments and analysis of the medium, generally, if the mechanical impurity content of the medium exceeds 1% by centrifugation, the electric field will fluctuate frequently or even collapse and it will be difficult to recover. Therefore, in the free water remover section, choosing targeted demulsifying agents to break this difficult-to-treat emulsion layer is very helpful for the subsequent stable operation of the electric field.
3.2 Application of oil-soluble demulsifiers
In the actual production process, many joint stations often experience frequent electric field fluctuations, inability to restore the reverse electric field, or inability to operate for a long time after restoration. These situations are usually caused by major changes in the comprehensive incoming liquid medium in front. One of the more obvious examples is the comprehensive incoming liquid from the sewage station that is transported to the joint station through the transfer station. This part of the medium is the oil layer stored on the top of the sedimentation tank after long-term sedimentation in the daily sewage system. In addition to conventional substances such as petroleum hydrocarbons, colloids, asphaltene, wax, solid particles, inorganic salts and bacteria, this part of the oil also contains polymers, alkalis, and surfactants for oil displacement. It is difficult to treat. Usually, it is still not ideal after a period of demulsifier selection. At this time, an effective auxiliary treatment measure is to add a reagent injection point at the front end of the electric dehydrator, and an oil-soluble demulsifier is generally selected. Because the water content of crude oil in the comprehensive incoming liquid of the joint station will generally drop to less than 30% after a period of treatment, this data also meets the design parameters of the electric dehydrator for oil fields. According to the emulsion phase transition theory, when the water content is less than 26%, W/O emulsion may be formed, so this part of the medium is mainly oil-in-water emulsion. The oil-soluble demulsifier is in the oil phase in molecular state, and its movement to the emulsion droplet interface is pure molecular diffusion movement, while the water-soluble demulsifier must undergo redistribution from the water phase to the oil phase before it can diffuse to the emulsion droplet interface. It should complete two basic types of diffusion movements, namely molecular diffusion and convective diffusion or directed turbulent diffusion. Therefore, when targeting W/O emulsions, the use of oil-soluble demulsifiers can better exert the dehydration effect.
4 Conclusion
Oilfield chemicals play a huge role in the oil and gas gathering and transportation system of oilfields. Due to the continuous updating of mining technology and the continuous changes in the produced fluid medium, higher requirements are also placed on the application of chemicals. Only by comprehensively analyzing scientific experiments based on different media and on-site process characteristics can chemical agents achieve the best results.
Demulsifiers Supplier
UNPChemicals is a professional oilfield chemical manufacturer, with products covering drilling, completion, oil production, gathering and transportation, etc., and has won the trust of customers with advanced technology, strict quality control and high-quality services. We are committed to personalized solutions to help oilfields develop efficiently.
UNPChemicals' Demulsifiers
DEMETâ„¢ A-21 demulsifier is a liquid oxyalkylate category, utilized in the industrial market for crude oil desalting processes, particularly in exploration and upstream applications.
DEMETâ„¢ C-232 demulsifier is a resin oxyalkylate intermediate utilized predominantly as a Water Dropper in oilfield production. It is also occasionally employed as a Dryer and an Interface Control Agent. It is effective for a broad spectrum of API crudes globally, including those in low-temperature scenarios.
DEMETâ„¢ C-168 demulsifier, a resin oxyalkylate intermediate, is primarily utilized in oilfield production as a Water Dropper, and also serves as a Dryer and Interface Control Agent for a broad spectrum of API crudes worldwide, including those in low-temperature environments.