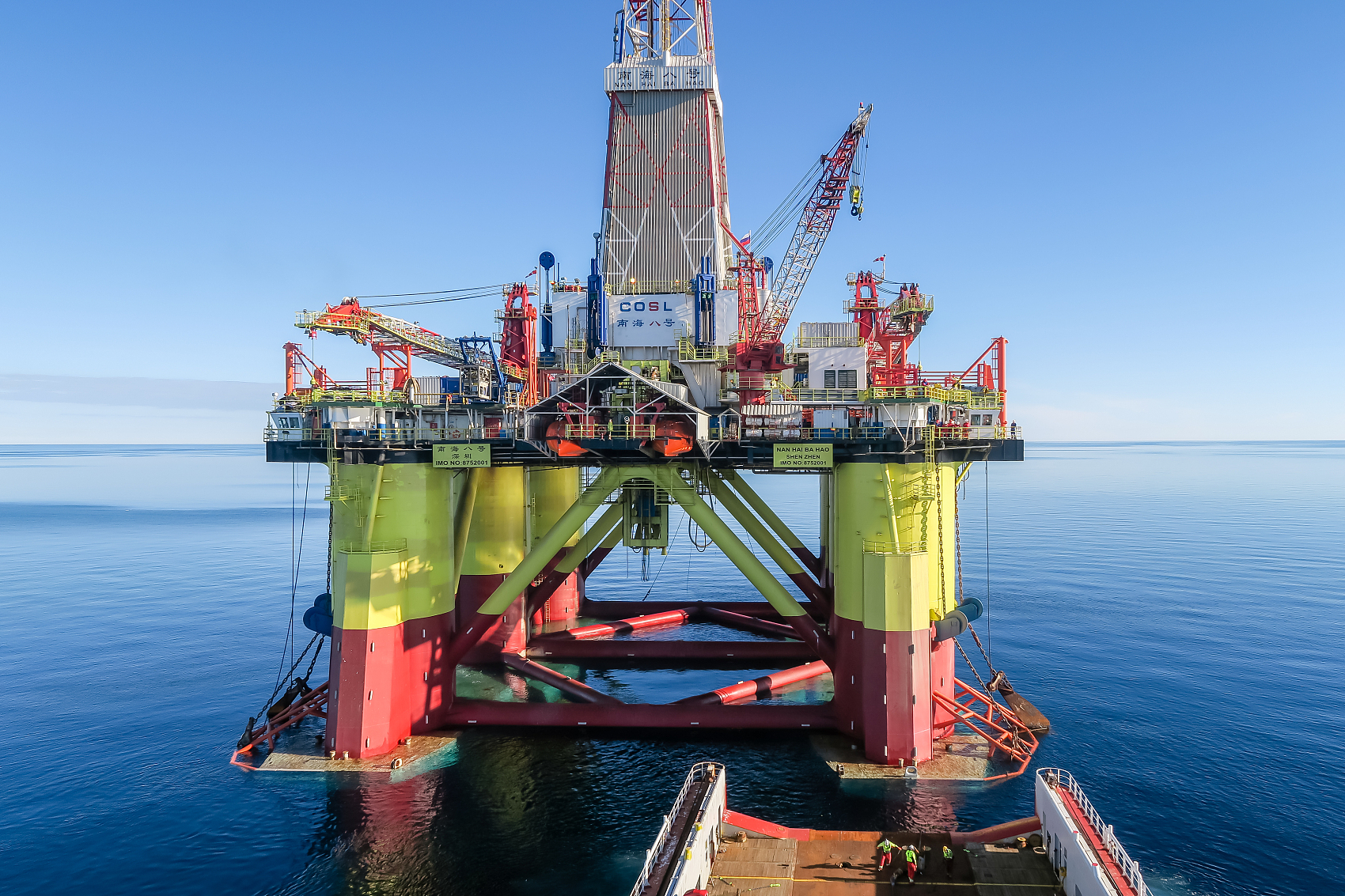
Advanced Paraffin Inhibitors for Oilfield Production: Chemistry, Applications, and Operational Strategies in Petroleum Gathering Systems
1. Fundamental Principles of Paraffin Deposition and the Role of Paraffin Inhibitors in Oilfield Operations
Paraffin deposition represents one of the most persistent flow assurance challenges in petroleum production systems, particularly in crude oil gathering networks and surface facilities where temperature conditions frequently fall below the wax appearance temperature (WAT) of the produced fluids. This phenomenon occurs when high molecular weight n-alkanes (typically C18-C60) dissolved in the crude oil begin to crystallize and precipitate as temperature decreases along the production flow path, forming complex three-dimensional networks that incorporate branched rmodynamic princples, beginning with nucleation of paraffin crystals at temperatures 5-15°C below the WAT (which can range from 20-60°C depending on crude composition), followed by crystal growth and eventual deposition on metal surfaces through mechanisms involving molecular diffusion, shear dispersion, and Brownian motion. Paraffin inhibitors, as specialized chemical additives, function through multiple sophisticated mechanisms to disrupt this deposition sequence: they modify crystal morphology by adsorbing onto nascent paraffin nuclei and preventing further anisotropic growth into plate-like structures; they alter the surface properties of pipeline materials to reduce wax adhesion strength by 60-80%; and in some advanced formulations, they maintain wax molecules in a pseudo-soluble state through steric stabilization effects. The economic imperative for effective paraffin control is substantial—unmitigated deposition can reduce production rates by 30-50% within months, while remediation through mechanical pigging or hot oiling treatments typically costs 50,000−200,000 per incident for offshore platforms, not accounting for production losses. Modern paraffin inhibitor technologies have consequently evolved into highly tailored solutions that must address specific crude oil characteristics (e.g., carbon number distribution of n-alkanes, asphaltene content, and resin-to-wax ratio), production temperatures, and flow regimes while maintaining compatibility with other production chemicals such as corrosion inhibitors and hydrate suppressants.
2. Comprehensive Classification of Paraffin Inhibitors Based on Chemical Structure and Mechanism of Action
The chemical diversity of paraffin inhibitors reflects the complexity of wax deposition phenomena, with commercial products generally categorized into four primary classes based on their molecular architecture and dominant inhibition mechanisms:
2.1 Polymeric Alkyl Acrylate/Ethylene Vinyl Acetate (EVA) Copolymers
These represent the most widely deployed paraffin inhibitors, particularly effective for crude oils with WAT between 30-50°C. The general chemical structure of a typical acrylate copolymer can be represented as:
where R is a C12-C22 alkyl group that provides hydrocarbon solubility and wax crystal interaction sites. The performance optimization involves careful balancing of the alkyl chain length (C18 chains show maximum efficacy for crude oils with dominant C25-C35 paraffins), vinyl acetate content (typically 5-15 mol% for crystallinity control), and molecular weight (optimum 5,000-15,000 Da for adequate diffusion to crystal growth sites). Field experience demonstrates that these copolymers can reduce wax deposition rates by 70-90% at treatment concentrations of 50-200 ppm, with the added benefit of lowering the pour point of treated crude by 5-15°C through crystal modification effects.
2.2 Comb-Type Polymers with Crystalline and Amorphous Segments
A newer generation of paraffin inhibitors employs precisely engineered comb-type architectures where long alkyl side chains (C16-C24) provide wax interaction sites while polar backbone segments (often containing maleic anhydride or sulfonate groups) ensure solubility and surface activity. These polymers exhibit superior performance in high-paraffin crudes (WAT >50°C) by:
Inserting their alkyl branches into the growing wax crystal lattice, creating structural defects that prevent further ordered growth
Forming protective surface layers on pipeline walls through polar group interactions
Maintaining effectiveness over wider temperature ranges (20-80°C) compared to conventional inhibitors
2.3 Nanocomposite Paraffin Inhibitors
Incorporating 1-5% surface-modified nanoparticles (typically silica or alumina with hydrophobic coatings) into traditional polymer inhibitors has shown remarkable improvements in:
Shear stability under high flow velocities (>3 m/s)
Long-term inhibition persistence (up to 30 days after single treatment)
Performance in high-shear devices like chokes and valves
2.4 Bio-Based Inhibitors
Derived from plant oils or microbial fermentation products, these environmentally acceptable alternatives are gaining traction in sensitive operating areas. Key examples include:
Sorbitan monooleate derivatives that modify crystal morphology
Lignin-based polymers providing both inhibition and dispersancy
Enzymatic systems that selectively degrade long-chain n-alkanes
3. Strategic Applications of Paraffin Inhibitors in Oilfield Operations
Paraffin inhibitors play a critical role in maintaining flow assurance across various stages of petroleum production, with tailored applications designed to address specific operational challenges. In downhole environments, continuous injection systems deliver optimized inhibitor formulations directly into the production string, typically through capillary tubing or side-pocket mandrels. These systems maintain active chemical concentrations of 100-500 ppm in the produced fluid, effectively preventing wax deposition from the moment hydrocarbons exit the formation. The selection of downhole inhibitors requires careful consideration of thermal stability, with specialized polymeric formulations capable of withstanding bottomhole temperatures exceeding 120°C while maintaining consistent performance over extended periods.
Pipeline applications demand different treatment strategies, where batch treatments using concentrated inhibitor "pills" are commonly employed in gathering systems. These periodic treatments involve pumping 5-15 barrels of inhibitor solution per pipeline mile at frequencies ranging from weekly to monthly, depending on crude characteristics and flow conditions. Advanced gel-based inhibitor systems have shown particular promise for pipeline applications, forming temporary viscous plugs that slowly release active components as they travel through the line, providing extended protection between treatments. Field results demonstrate that properly designed pipeline treatment programs can reduce pigging frequency by 50-70%, significantly lowering operational costs while maintaining flow efficiency.
Processing facilities present unique challenges for paraffin control, particularly at temperature transition points such as separator inlets and heat exchanger surfaces. Here, inhibitor formulations are often combined with dispersant components to prevent the accumulation of wax crystals in vessel bottoms and heat transfer surfaces. Modern facility applications increasingly utilize automated injection systems that adjust chemical dosage based on real-time monitoring of process parameters, including temperature differentials and pressure drops across critical equipment. Subsea flowlines represent perhaps the most challenging application environment, where specialized nanocomposite inhibitors provide long-lasting protection despite limited opportunities for intervention, with some formulations demonstrating effective inhibition for over six months between treatments in deepwater operations.
4. Implementation and Optimization of Paraffin Inhibition Programs
Effective paraffin control requires comprehensive laboratory evaluation prior to field implementation, employing standardized test protocols to verify inhibitor performance under simulated field conditions. The wax appearance temperature (WAT) reduction test using differential scanning calorimetry provides critical data on a formulation's ability to depress the onset of crystallization, while cold finger apparatus measurements quantify deposition rates under controlled shear and temperature conditions. Advanced analytical techniques such as cross-polarized microscopy reveal the morphological changes induced in wax crystals by different inhibitor chemistries, enabling precise matching of products to specific crude oil characteristics. These laboratory studies typically evaluate multiple candidate formulations across a range of concentrations and temperature profiles to identify the optimal treatment strategy.
Field implementation begins with careful design of chemical injection systems, selecting appropriate injection points based on fluid dynamics and temperature profiles throughout the production system. Continuous injection systems require precise metering pumps and distribution manifolds to ensure consistent chemical delivery, while batch treatment programs must account for pipeline geometry and flow rates to achieve proper inhibitor distribution. Modern monitoring techniques have revolutionized paraffin control programs, with ultrasonic thickness gauges providing direct measurement of deposit accumulation and infrared spectroscopy enabling real-time analysis of wax content in flowing streams. These monitoring approaches feed into increasingly sophisticated control algorithms that dynamically adjust treatment parameters, optimizing chemical usage while maintaining system cleanliness.
Performance tracking forms the foundation of continuous improvement in paraffin control programs, with key metrics including pigging frequency, pressure drop trends, and chemical consumption rates. Advanced operators employ machine learning techniques to analyze historical performance data, identifying correlations between operational parameters and treatment effectiveness that guide ongoing optimization efforts. This data-driven approach has enabled reductions in paraffin control costs of 20-40% at many operations, while simultaneously improving system reliability and reducing unplanned interventions. The integration of paraffin inhibition programs with broader flow assurance strategies has become standard practice in modern oilfield operations, ensuring comprehensive protection against all forms of production impairment.
5. Market Economics and Cost Optimization
5.1 Price Structures by Inhibitor Class
5.2 Cost-Saving Strategies
Formulation Optimization: Matching inhibitor chemistry to crude characteristics
Precision Injection Systems: Minimizing chemical overuse
Performance-Based Contracts: Aligning supplier incentives with operational results
Paraffin Inhibitors Supplier
UNPChemicals is a professional oilfield chemical manufacturer, with products covering drilling, completion, oil production, gathering and transportation, etc., and has won the trust of customers with advanced technology, strict quality control and high-quality services. We are committed to personalized solutions to help oilfields develop efficiently.