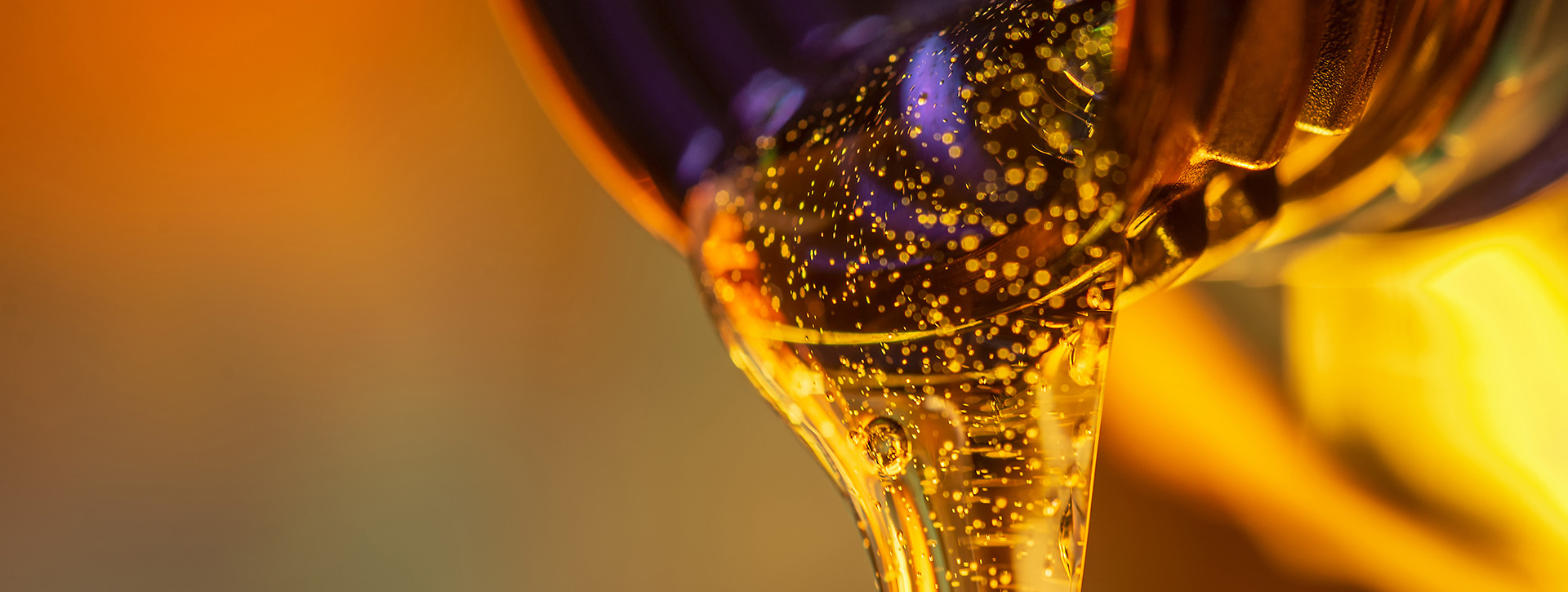
Study on the Performance of Hydraulic Oil Composite Additives Under High-Temperature Environments
In the modern industrial field, hydraulic systems are widely used in various industries such as metallurgy, machinery manufacturing, aerospace, and mining due to their advantages of high power density, stable transmission, and rapid response. However, in many industrial scenarios, hydraulic systems often need to operate in high-temperature environments, such as rolling equipment in steel mills, hydraulic devices in automobile engine compartments, and hydraulic control systems near aero-engines. High-temperature environments pose severe challenges to hydraulic systems, and hydraulic oil, as the "blood" of hydraulic systems, its performance directly determines the working state and service life of the system. As a key component to improve the performance of hydraulic oil, hydraulic oil composite additives will have significant impacts on their own chemical stability, oxidation resistance, viscosity retention, and other performance indicators in high-temperature environments, which in turn lead to the degradation of hydraulic oil performance, causing problems such as leakage, increased wear, reduced efficiency, and even failures in hydraulic systems. Therefore, in-depth research on the performance change rules of hydraulic oil composite additives in high-temperature environments and exploration of effective measures to improve their high-temperature performance are of great theoretical significance and practical application value for ensuring the safe and stable operation of hydraulic systems in high-temperature environments.
1. Impact of High Temperature on the Performance of Hydraulic Oil Composite Additives
1.1 Impact of Oxidation
High-temperature environments will significantly accelerate the oxidation reaction of hydraulic oil composite additives. Hydraulic oil composite additives contain a variety of components, such as base oil, antioxidants, anti-wear agents, detergents and dispersants, etc. Under high-temperature conditions, these components will undergo a series of complex oxidation reactions when in contact with oxygen in the air. Oxidation reactions will generate acidic substances, which will corrode the metal parts of the hydraulic system, damage the performance of sealing materials, and lead to system leakage. At the same time, oxidation reactions will also produce sediments such as sludge and paint films, which will block the pipelines, filters, and throttle valves of the hydraulic system, affect the flow performance of hydraulic oil, and reduce the working efficiency of the system. In addition, the chemical structure of the oxidized hydraulic oil composite additive changes, which will lead to a significant decline in its key performance indicators such as oxidation resistance and anti-wear properties, shortening the service life of hydraulic oil.
1.2 Impact of Viscosity Change
Viscosity is one of the important performance indicators of hydraulic oil, which directly affects the transmission accuracy and energy loss of the hydraulic system. In high-temperature environments, the viscosity of hydraulic oil composite additives will decrease with the increase of temperature. This is because high temperature increases the distance between the molecules of the composite additive, weakens the intermolecular forces, and leads to enhanced fluidity. When the viscosity of hydraulic oil decreases to a certain extent, it will reduce the volumetric efficiency of the hydraulic pump, increase the system pressure fluctuation, and make the action of the actuators slow and unstable. At the same time, the decrease in viscosity will also lead to a thinner oil film formed by hydraulic oil on the surface of the friction pair, which is difficult to effectively isolate the metal surfaces, increasing the wear of parts and reducing the service life of the system. In addition, excessive viscosity reduction may also cause cavitation in the hydraulic system, generating noise and vibration, and further exacerbating system damage.
1.3 Impact on Other Performances
In addition to oxidation and viscosity changes, high temperature will also have adverse effects on other performances of hydraulic oil composite additives. For example, high temperature will inactivate the anti-wear agents in the composite additives. Anti-wear agents reduce wear by forming a protective film on the metal surface, but high temperature will destroy the stability of this protective film, making it lose its anti-wear effect. At the same time, high temperature will also affect the defoaming performance of the composite additive. During the operation of the hydraulic system, it is inevitable to mix with air to generate bubbles. The role of defoamers is to make the bubbles break quickly, but high temperature will reduce the activity of defoamers, causing bubbles to accumulate in the system, affecting the transmission efficiency of hydraulic oil, and even causing cavitation. In addition, high temperature may also reduce the flash point of the hydraulic oil composite additive, increasing the risk of fire and explosion in the system.
2. Measures to Improve High-Temperature Performance
2.1 Selection of Additives
Selecting appropriate additives is one of the key means to improve the high-temperature performance of hydraulic oil composite additives. To address the oxidation problem at high temperatures, high-efficiency antioxidants should be used. Antioxidants can delay the oxidation process of hydraulic oil composite additives by capturing free radicals and terminating oxidation chain reactions. Common high-efficiency antioxidants include amine antioxidants and phenolic antioxidants. Among them, amine antioxidants have more prominent antioxidant effects at high temperatures but are relatively expensive; phenolic antioxidants have good stability and compatibility and are suitable for various hydraulic oil systems.
To improve the viscosity performance at high temperatures, viscosity index improvers can be added. Viscosity index improver is a kind of polymer. At low temperatures, its molecules curl into spheres, which have little effect on the viscosity of the oil; at high temperatures, the molecules stretch into chains, increasing the viscosity of the oil, so that the hydraulic oil can maintain relatively stable viscosity in a wide temperature range. Common viscosity index improvers include polymethacrylate and polyisobutylene. When selecting, it is necessary to reasonably match according to the base oil type and operating temperature range of the hydraulic oil.
In addition, anti-wear additives can be added to enhance the anti-wear performance of the composite additive at high temperatures, such as sulfur-phosphorus anti-wear agents, which can chemically react with the metal surface at high temperatures to form a hard chemical protective film, effectively reducing wear. At the same time, adding defoamers and anti-foaming agents can improve the defoaming performance of the composite additive. Choosing high-temperature resistant defoamers, such as organosilicon defoamers, can maintain good defoaming effect in high-temperature environments.
2.2 Formula Optimization
It is not enough to only select appropriate additives; it is also necessary to optimize the formula of the hydraulic oil composite additive to achieve the synergistic effect between various additives and achieve the best high-temperature performance. In the process of formula optimization, it is necessary to consider the proportion and compatibility of each additive. Different additives may produce synergistic or antagonistic effects. For example, when some antioxidants and anti-wear agents are used together, their antioxidant and anti-wear properties will be better than when used alone; while some additives will interfere with each other, reducing their respective performances. Therefore, it is necessary to determine the optimal proportion of each additive through a large number of experimental studies.
At the same time, formula optimization also needs to consider the selection of base oil. Base oil is the main component of hydraulic oil composite additive, and its performance has an important impact on the high-temperature performance of the composite additive. Base oils with high viscosity index, high flash point, and good oxidation stability should be selected. For example, polyalphaolefin oil in synthetic base oils has excellent high-temperature stability and oxidation stability, which can provide good basic performance for composite additives. Combining appropriate base oil with optimally proportioned additives can significantly improve the high-temperature performance of hydraulic oil composite additives.
In addition, in the process of formula optimization, it is also necessary to consider the specific operating conditions of the hydraulic system, such as operating temperature, operating pressure, load size, etc. Adjust the formula of the composite additive according to different working conditions to make it adapt to specific high-temperature environments and play the best performance.
3. Conclusion
3.1 Performance Characteristics of Hydraulic Oil Composite Additives in High-Temperature Environments
Based on the above research, it can be seen that the performance of hydraulic oil composite additives will be adversely affected in many aspects in high-temperature environments. The oxidation reaction is intensified, leading to increased acid value and sludge formation, corroding system parts and blocking oil circuits; the viscosity decreases significantly, affecting the transmission accuracy and lubrication effect of the system, and increasing part wear; the performance of additives such as anti-wear agents and defoamers decreases, further reducing the overall performance of the composite additive. Different formulations of hydraulic oil composite additives have different performance in high temperatures. Those composite additives that use high-efficiency antioxidants, high-quality viscosity index improvers, and have reasonable formula optimization have better performance in viscosity retention, oxidation stability, and anti-wear properties at high temperatures.
3.2 Improvement Directions
To further improve the performance of hydraulic oil composite additives in high-temperature environments, future improvements can be made in the following aspects. First, develop new and efficient additives, such as antioxidants with higher antioxidant activity and thermal stability, and viscosity index improvers that can maintain viscosity stability in a wider temperature range. Second, optimize the formula design of the composite additive, in-depth study the synergistic mechanism between different additives, and maximize the performance of each additive through reasonable proportioning. Third, strengthen the research and development of base oils, find base oils with better high-temperature performance, and provide a more solid foundation for the high-temperature performance of composite additives. Fourth, combine the specific working conditions of the hydraulic system to develop special high-temperature hydraulic oil composite additives to meet the special needs of different industries for hydraulic systems in high-temperature environments. Through these improvement measures, it is expected to significantly improve the performance of hydraulic oil composite additives in high-temperature environments, ensure the safe and stable operation of hydraulic systems, and extend their service life.
The Price of Hydraulic Oil Additives Package
The price of Hydraulic Oil Additives Package varies depending on factors such as brand, specification, composition, and sales channels. If you are interested in Hydraulic Oil Additives Package, please feel free to contact us.
Supplier of Hydraulic Oil Additives Package
UNPChemicals is a professional supplier of high-quality and effective Hydraulic Oil Additives Package. We offer several remarkable products, namely High zinc hydraulic oil additives UNP AH502A,Low Zinc Hydraulic Oil Additives UNP AH502B,Zinc-free Hydraulic Oil Additives UNP AH502C,etc.
High zinc hydraulic oil additives UNP AH502A are a type of chemical additive used in hydraulic oils that contain high levels of zinc dialkyldithiophosphate (ZDDP). ZDDP is a well-known anti-wear agent that also provides antioxidant, anti-corrosion, and anti-foam properties. The zinc in these additives plays a crucial role in forming a protective film on metal surfaces within the hydraulic system, thereby reducing wear and extending the life of the system components.
Low Zinc Hydraulic Oil Additives UNP AH502B are a class of advanced lubricant additives designed to enhance the performance of hydraulic oils with reduced zinc content.These additives are formulated to provide a balance of anti-wear,extreme pressure,and antioxidant properties,making them suitable for modern hydraulic systems that demand high performance with lower environmental impact.
Zinc-free Hydraulic Oil Additives UNP AH502C are a new class of environmentally friendly lubricant additives designed for hydraulic systems.These additives are formulated to provide the same level of performance as traditional zinc-containing additives but without the heavy metal content,reducing the environmental impact of hydraulic fluids.
Professional Lubricant Additive Manufacturer
UNPChemicals,aka Luoyang Pacific United Petrochemical Co., Ltd., focuses on the application and development of special lubricating grease additives such as MODTC, MODTP, molybdenum amide, thiadiazole metal deactivators, and phosphate esters. With nearly 30 products in seven series, including extreme pressure anti-wear additives and special grease additives, it is a global manufacturer of special lubricating grease additives and a national high-tech enterprise with great influence and leading role in the industry. If you are looking for Lubricant Additive or technical information, feel free to contact UNPChemicals.